A rubber injection molding machine is a specialized piece of equipment used in the manufacturing process of rubber products.
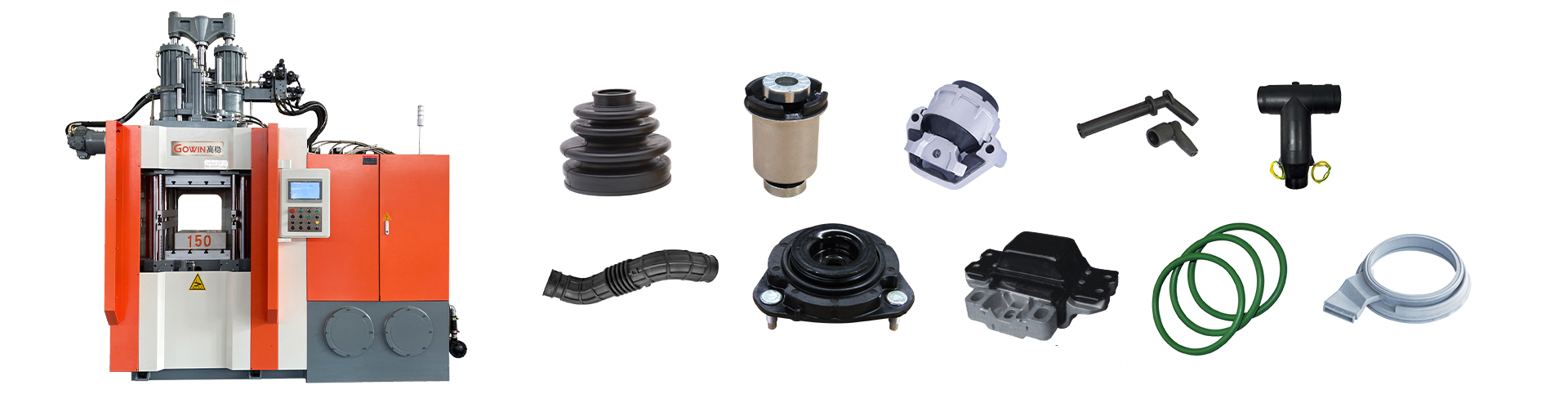
1.Working Principle
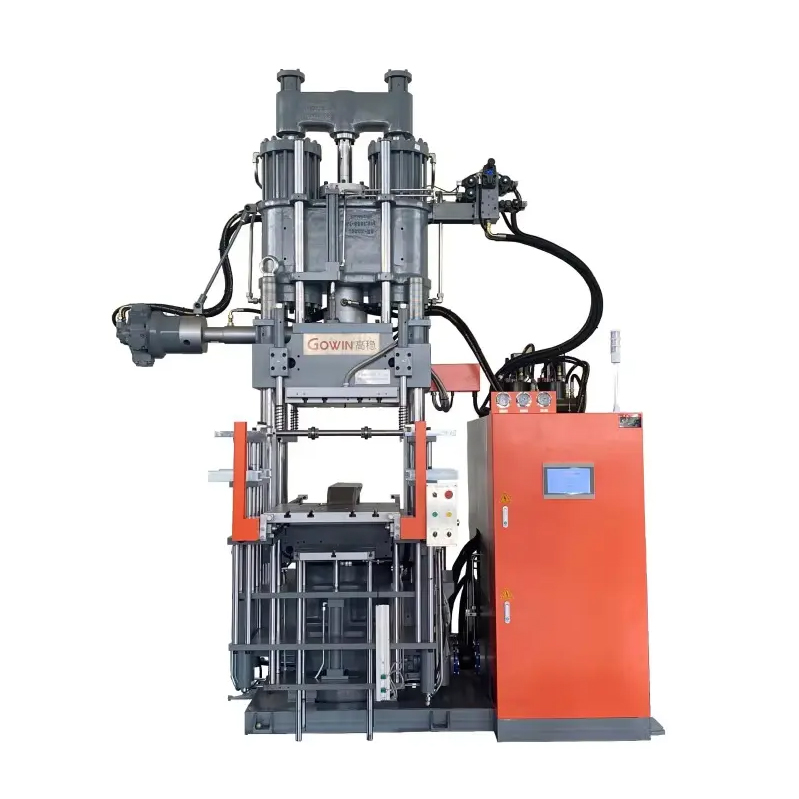
- (1)It operates by first melting or plasticizing the rubber material. The rubber is usually in the form of pellets or pre - formed blanks. These are fed into a heated barrel through a hopper. Inside the barrel, a screw - like mechanism rotates and moves the rubber forward. As the rubber travels through the barrel, it is heated and softened to a viscous state.
- (2)Once the rubber reaches the proper consistency, it is then injected under high pressure through a nozzle into a closed mold cavity. The mold is designed in the shape of the desired rubber product. The high - pressure injection ensures that the rubber fills every part of the mold cavity precisely, replicating the shape of the mold.
2.Components of a Rubber Injection Molding Machine
- Hopper: This is where the raw rubber material is loaded. It provides a reservoir for the rubber pellets or blanks to be fed into the machine.
- Barrel and Screw: The barrel is a heated chamber. The screw inside rotates and conveys the rubber through the barrel. The screw also helps in mixing and homogenizing the rubber as it moves forward. The heating of the barrel is usually controlled by heating elements that can adjust the temperature according to the specific requirements of the rubber being processed.
- Nozzle: The nozzle is the part through which the molten rubber is injected into the mold. It is designed to provide a smooth and controlled flow of the rubber into the mold cavity.
- Mold Clamping Unit: This part of the machine holds the two halves of the mold together tightly during the injection process. The clamping force is essential to prevent the mold from opening due to the high injection pressure of the rubber. The clamping unit can be hydraulic, mechanical, or a combination of both, depending on the design of the machine.
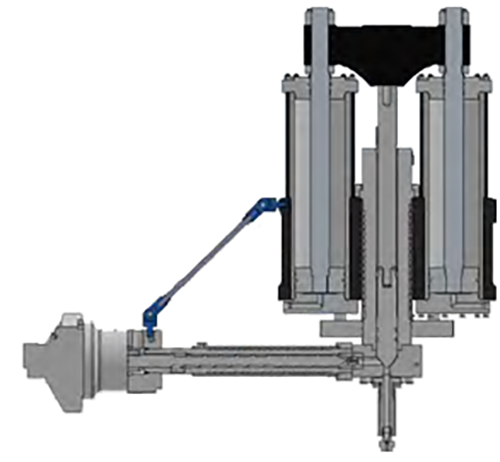
3. Advantages of Rubber Injection Molding Machines
- High Precision: It can produce rubber products with complex shapes and very precise dimensions. The high - pressure injection allows for fine details and accurate replication of the mold design. For example, in the production of rubber seals for automotive engines, the injection molding process can ensure a perfect fit and seal.
- High Productivity: These machines can operate at a relatively high cycle speed. Once the mold is set up, multiple parts can be produced in a short period of time. This makes it suitable for mass - production operations, such as the manufacturing of rubber gaskets for industrial equipment.
- Good Material Utilization: The injection process allows for better control of the amount of rubber used. There is less waste compared to some other molding methods, as the exact amount of rubber needed to fill the mold cavity can be precisely injected.
4. Applications
- Automotive Industry: Used to produce a wide range of rubber parts such as seals, gaskets, bushings, and grommets. These components are crucial for the proper functioning of vehicles, providing sealing and vibration - damping functions.
- Medical Equipment: In the production of rubber components for medical devices like syringes, tubing connectors, and seals for medical equipment. The precision of injection molding is vital to ensure the safety and functionality of these medical products.
- Consumer Goods: Produces rubber parts for various consumer products such as toys, footwear, and household appliances. For example, the rubber soles of shoes or the buttons on a remote - control can be made using a rubber injection molding machine.
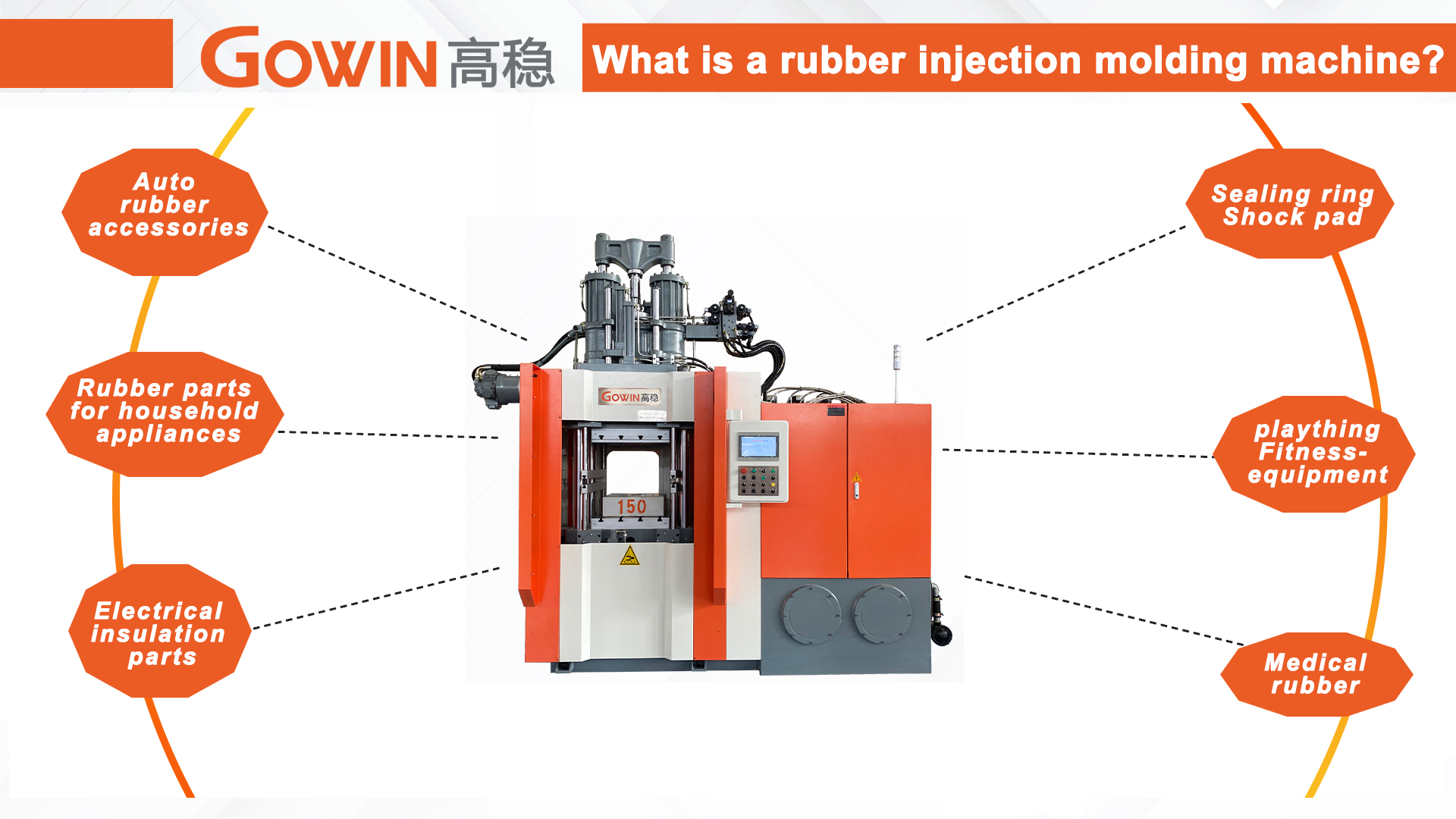
Post time: Oct-29-2024