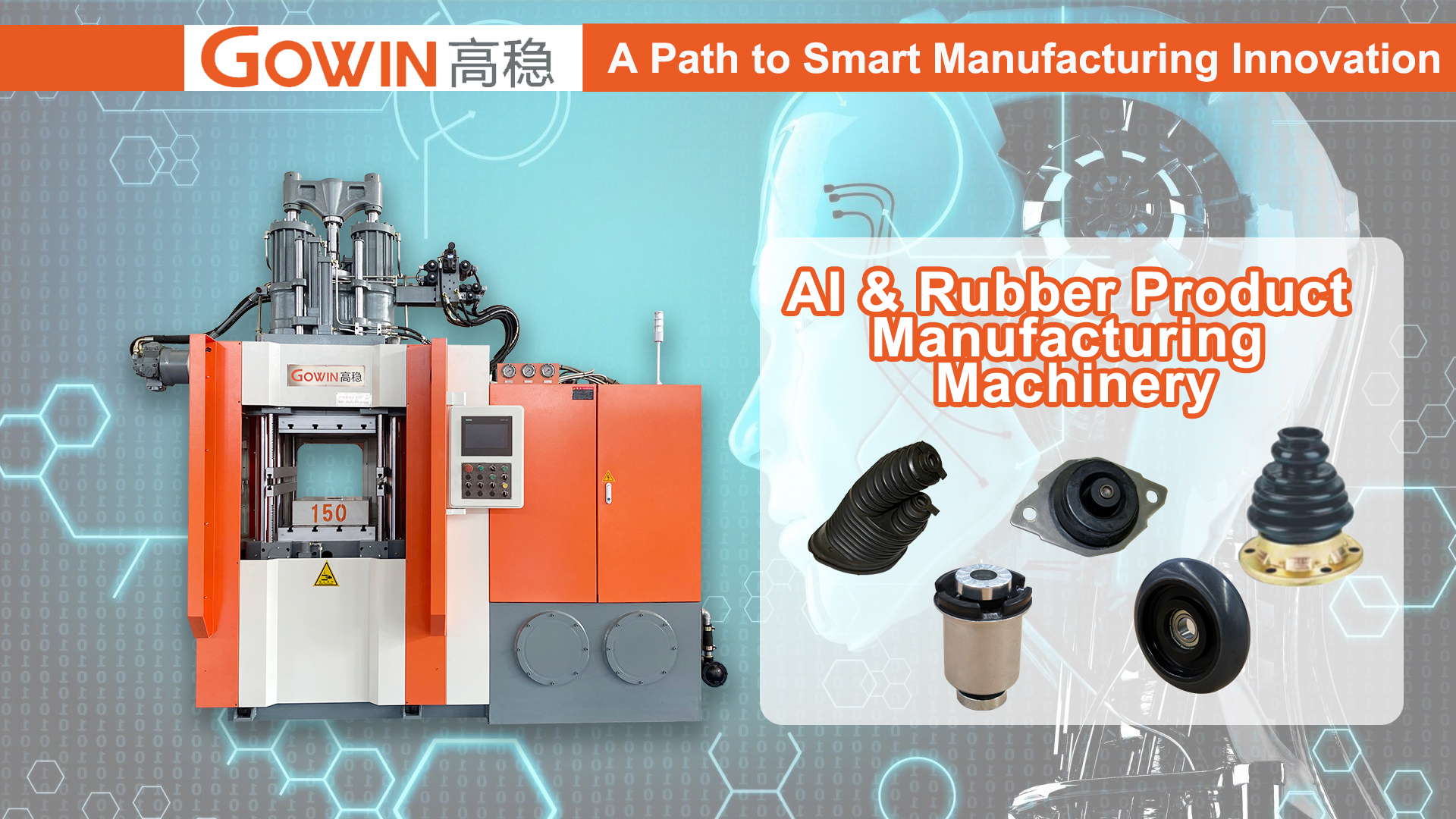
Against the backdrop of global manufacturing's shift toward automation and intelligence, the rubber product manufacturing industry is undergoing its own technological revolution. With the rapid development of Artificial Intelligence (AI), it is now deeply integrated with rubber manufacturing machinery, driving improvements in production efficiency, product quality, and cost control.
From automated production lines to smart monitoring systems, from predictive maintenance to customized production, AI is gradually penetrating every stage of rubber manufacturing, reshaping the industry's future. In this article, we explore key applications of AI in rubber product manufacturing machinery and the profound impact this integration is having on the industry.
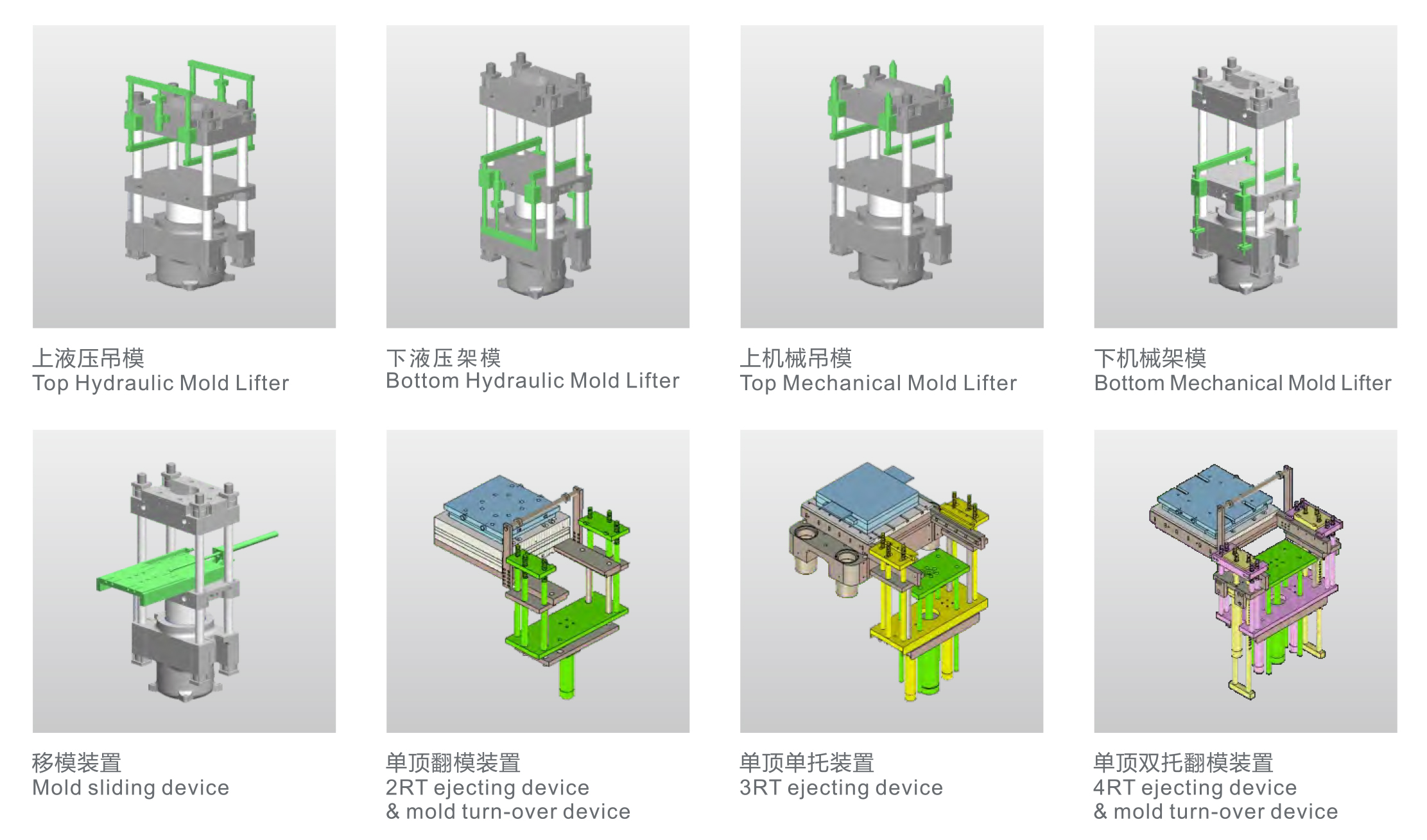
1. Intelligent Production Process Optimization: Enhancing Efficiency and Precision
The production of rubber products involves several complex stages, such as mixing, vulcanization, and molding. Key parameters like temperature, pressure, mixing ratios, and time are critical to the final product's quality. AI can optimize these processes by continuously analyzing real-time data and automatically adjusting the machine settings based on production conditions.
For example, in the rubber mixing process, AI systems can precisely adjust the blend of materials to ensure each batch meets optimal conditions, reducing human error and waste. During the vulcanization process, AI analyzes temperature, time, and pressure fluctuations to predict the reaction’s progress and adjust the machine parameters automatically, ensuring consistent quality across every batch.
Through this intelligent optimization, rubber manufacturers can improve production efficiency and maintain high-quality standards, gaining a competitive advantage in the market.
2. Predictive Maintenance: Reducing Downtime and Extending Equipment Lifespan
Equipment failure and downtime are common challenges in traditional production environments. In rubber manufacturing, machinery such as mixers, vulcanizers, and calenders are central to production. Any malfunction can lead to production halts and costly repairs.
AI addresses this by leveraging smart sensors and data acquisition systems to continuously monitor equipment performance. Through machine learning algorithms, AI can analyze these data points and predict potential failures. For example, AI can detect issues such as motor overheating, excessive wear, or high system pressure, providing early warnings for maintenance.
With predictive maintenance, AI significantly reduces unexpected downtime and helps manufacturers optimize maintenance schedules. This leads to longer equipment lifespans and lower maintenance costs, ultimately enhancing overall production efficiency.
3. Automated Quality Inspection: Precisely Identifying Defects and Improving Production Quality
Quality control is one of the most critical aspects of rubber product manufacturing. From visual inspection to dimensional accuracy, traditional manual quality checks are often inefficient and prone to errors due to human factors, fatigue, or subjective bias.
AI, combined with computer vision technology, offers a solution to this challenge. By using high-precision cameras and sensors, AI systems can perform real-time quality inspections of rubber products, detecting even the smallest cracks, bubbles, or dimensional discrepancies. Furthermore, AI can classify and analyze defects, identifying root causes to help the production team resolve issues quickly.
For example, AI can automatically categorize different types of defects, providing specific recommendations for process improvements. This automated quality inspection system is not only more efficient than traditional manual methods but also increases product consistency and reduces the rejection rate.
4. Flexible Customization: Meeting Personalized Demands
As consumer needs become more diverse, there is an increasing demand for customized rubber products. However, traditional production systems often struggle to quickly adapt to different specifications and models, leading to longer production cycles and higher costs.
AI enables highly flexible and automated production lines that can rapidly adjust production parameters to meet specific customer requirements. By integrating AI-driven smart scheduling and production optimization, manufacturers can switch between different orders and product specifications quickly, enabling small-batch, personalized production without significant manual intervention.
This smart manufacturing advantage allows rubber manufacturers to respond faster to complex customer demands while reducing inventory pressure and improving market agility.
5. Data-Driven Production Optimization: Lean Manufacturing and Cost Reduction
Data collection, analysis, and utilization have become essential for improving production efficiency and reducing costs in rubber manufacturing. AI, through the analysis of vast amounts of production data, can identify key factors impacting efficiency and quality, offering decision-making support for continuous improvement.
For instance, AI systems can analyze data from raw material usage, equipment performance, and production line loads to generate optimized production plans. This helps manufacturers reduce material waste, shorten production cycles, and avoid overproduction, ultimately lowering costs. Moreover, AI can optimize energy consumption, improving energy efficiency and reducing the overall cost of production.
6. Smart Supply Chain Management: Improving Resource Allocation Efficiency
The rubber manufacturing process is heavily dependent on an efficient and well-managed supply chain, from raw material procurement to product distribution. AI plays a critical role in optimizing supply chain operations by analyzing market demand, raw material supply, and transportation routes, ensuring that the necessary materials are available when needed while reducing inventory buildup.
AI can predict market demand fluctuations and adjust production and procurement plans accordingly, preventing raw material shortages or surpluses. This ensures smooth and timely production processes. Additionally, AI can optimize transportation routes and logistics scheduling, improving the overall efficiency of the supply chain and reducing transportation costs.
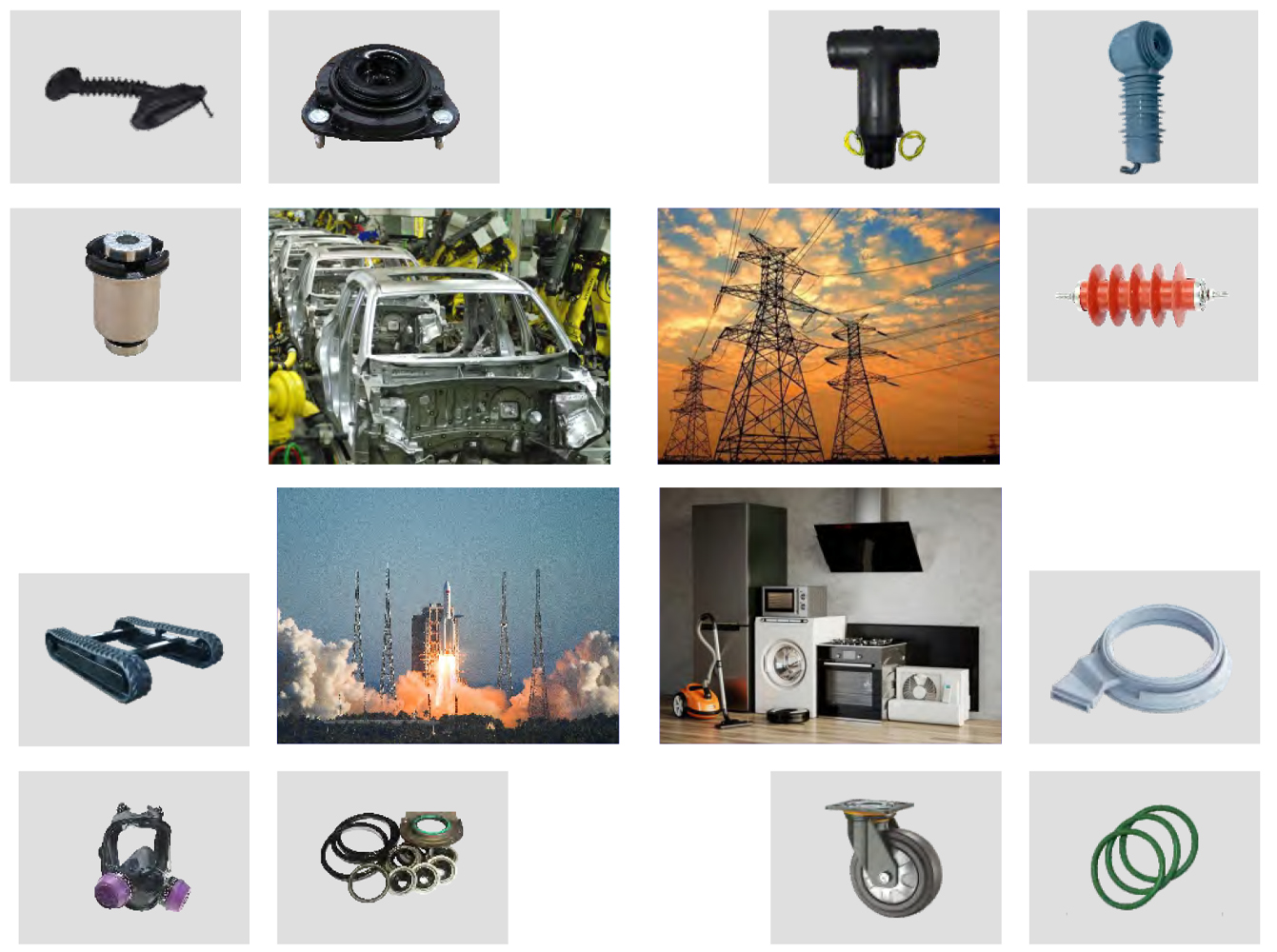
Conclusion: Embracing the Era of Smart Manufacturing
The integration of artificial intelligence with rubber product manufacturing machinery is ushering in a technological revolution for the industry. With AI’s ability to optimize production processes, enhance product quality, reduce costs, and improve supply chain efficiency, rubber manufacturers can stay competitive and meet the demands of a rapidly evolving market.
As AI technologies continue to mature and new applications emerge, the rubber manufacturing industry is set to become even more intelligent, flexible, and efficient. For industry stakeholders, embracing AI is not only crucial for maintaining competitiveness but also essential for long-term, sustainable growth.
The intelligent upgrade of rubber product manufacturing machinery is the inevitable future of the industry. Manufacturers who leverage AI’s capabilities will be well-positioned to succeed in the increasingly dynamic global marketplace.
Post time: Nov-29-2024