Technological breakthroughs of rubber injection machines are mainly reflected in the following aspects:
1. Improvement of injection system:
- Optimization of runner design: Traditional rubber injection runners may have designs such as bends, leading to increased pressure loss during rubber flow and affecting product quality and production efficiency. New technological breakthroughs are dedicated to optimizing runner design, reducing bends and branch runners to make rubber flow more smoothly and reduce pressure loss. For example, some new runner designs adopt straight or special arc structures to reduce the residence time of rubber in the runner and lower the risk of early vulcanization.
- Precise control of injection pressure and speed: Advanced rubber injection machines can achieve precise control of injection pressure and speed. By using high-precision sensors, advanced control systems, and servo drive technology, injection pressure and speed can be precisely adjusted according to different rubber materials and product requirements to ensure that rubber can evenly fill the mold cavity and improve the molding quality of products.
2. Innovation in molding technology:
- Multi-component injection molding: For some complex rubber products, it is necessary to inject multiple different rubber materials or add other functional materials simultaneously. The breakthrough in multi-component injection molding technology enables rubber injection machines to inject multiple materials at the same time and achieve precise distribution and combination of different materials in the mold, thereby producing rubber products with multiple properties, such as rubber seals and rubber shock absorbers with different hardnesses, colors, or functions.
- Micro molding technology: With the development of industries such as electronics and healthcare, the demand for micro-sized rubber products is constantly increasing. The breakthrough in micro molding technology enables rubber injection machines to produce micro rubber products with high dimensional accuracy and stable quality, such as micro rubber sealing rings and rubber catheters. This requires innovation in injection systems, mold design, and molding processes to ensure that rubber materials can accurately fill tiny mold cavities.
3. Application of intelligent control technology:
- Automated production: The degree of automation of rubber injection machines is constantly increasing, enabling fully automated production from raw material transportation, injection molding, vulcanization to product removal. By using equipment such as robots, automated conveying devices, and sensors, production efficiency can be improved, labor intensity can be reduced, and the impact of human factors on product quality can be minimized.
- Intelligent monitoring and fault diagnosis: With the help of intelligent sensors and big data analysis technology, rubber injection machines can monitor various parameters in the production process in real time, such as temperature, pressure, and injection speed, and analyze and process the data. When abnormal situations occur, alarms can be issued in time and fault diagnosis can be performed to help operators quickly troubleshoot and reduce downtime, improving the reliability and stability of the equipment.
4. Development of energy-saving technologies:
- Servo drive system: The application of servo drive systems in rubber injection machines is becoming more and more widespread. They can automatically adjust the motor speed and output power according to production needs to achieve energy saving and consumption reduction. Compared with traditional hydraulic drive systems, servo drive systems have higher energy conversion efficiency and lower energy consumption, and also have advantages such as fast response speed, high precision, and low noise.
- Thermal management technology: Rubber injection machines need to heat and vulcanize rubber materials during production, which requires a large amount of energy. Breakthroughs in thermal management technology include the use of efficient heating elements, optimized heating methods, and insulation measures, which can improve energy utilization efficiency and reduce energy consumption. For example, some new rubber injection machines adopt electromagnetic heating technology, which has the advantages of fast heating speed, good temperature uniformity, and significant energy-saving effects.
5. Enhancement of mold technology:
- Improvement of mold materials: Molds are key components in rubber injection molding, and their quality and performance directly affect the molding quality and production efficiency of products. New mold materials have higher hardness, strength, and wear resistance, can withstand higher injection pressures and temperatures, and prolong the service life of molds. At the same time, some special mold materials also have good thermal conductivity and demolding performance, which helps improve the production efficiency and quality of products.
- Optimization of mold structure: By using advanced design software and simulation technology, the mold structure can be optimized to improve the strength and stiffness of the mold and reduce mold deformation and wear. For example, using finite element analysis method to analyze and optimize the mold structure to determine the optimal mold structure and size and improve the reliability and stability of the mold.
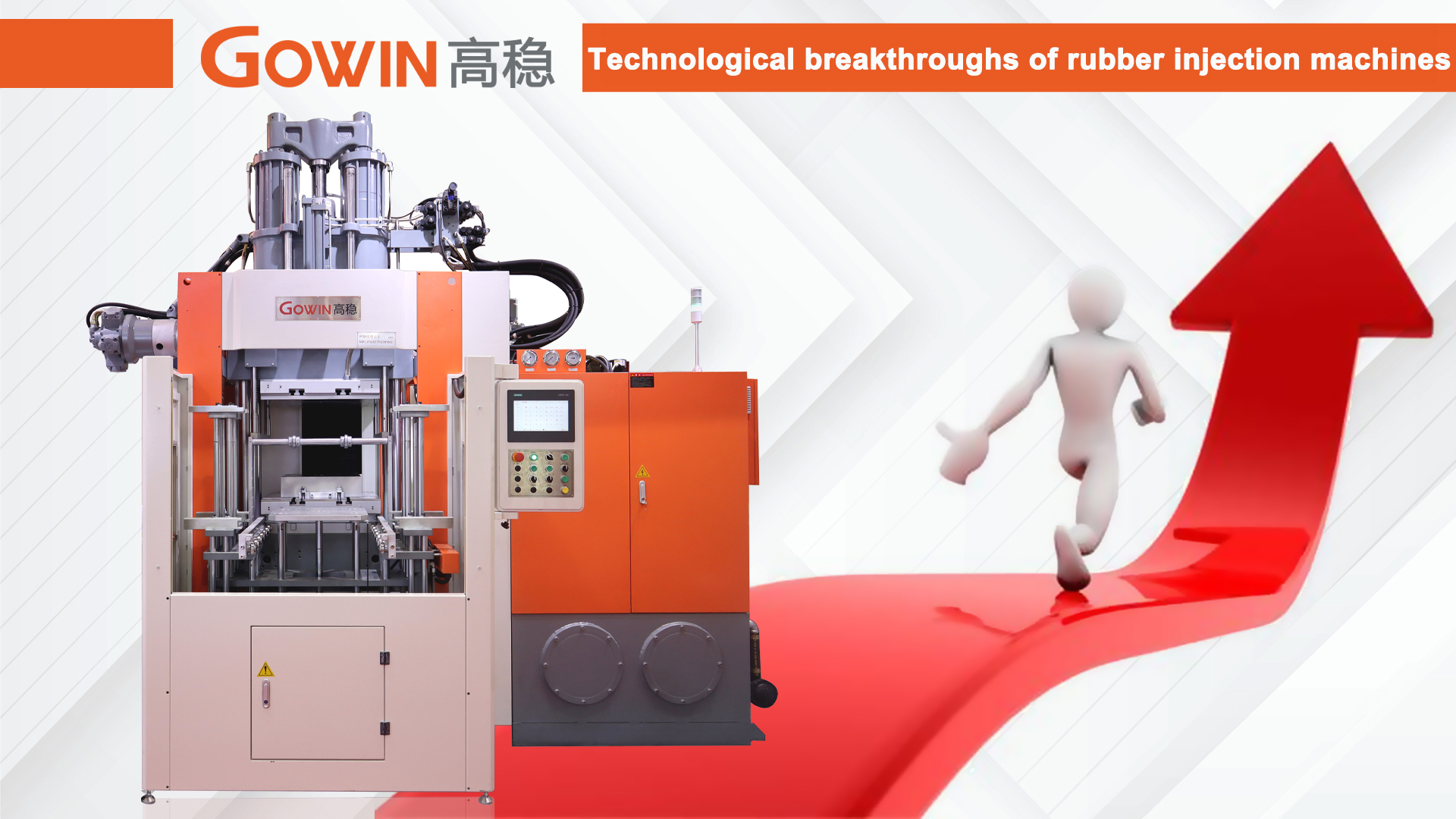
Post time: Oct-10-2024