As global awareness of environmental protection continues to rise, industries across the board are seeking more sustainable production methods. The rubber industry is no exception, with a growing focus on how to conserve resources, reduce emissions, and minimize energy consumption. In the field of rubber processing, rubber injection machines stand out as a key technology that not only enhances production efficiency but also offers significant environmental benefits. This article will explore the environmental impact of rubber injection machines and discuss the green technologies and practices that can help drive eco-friendly production.
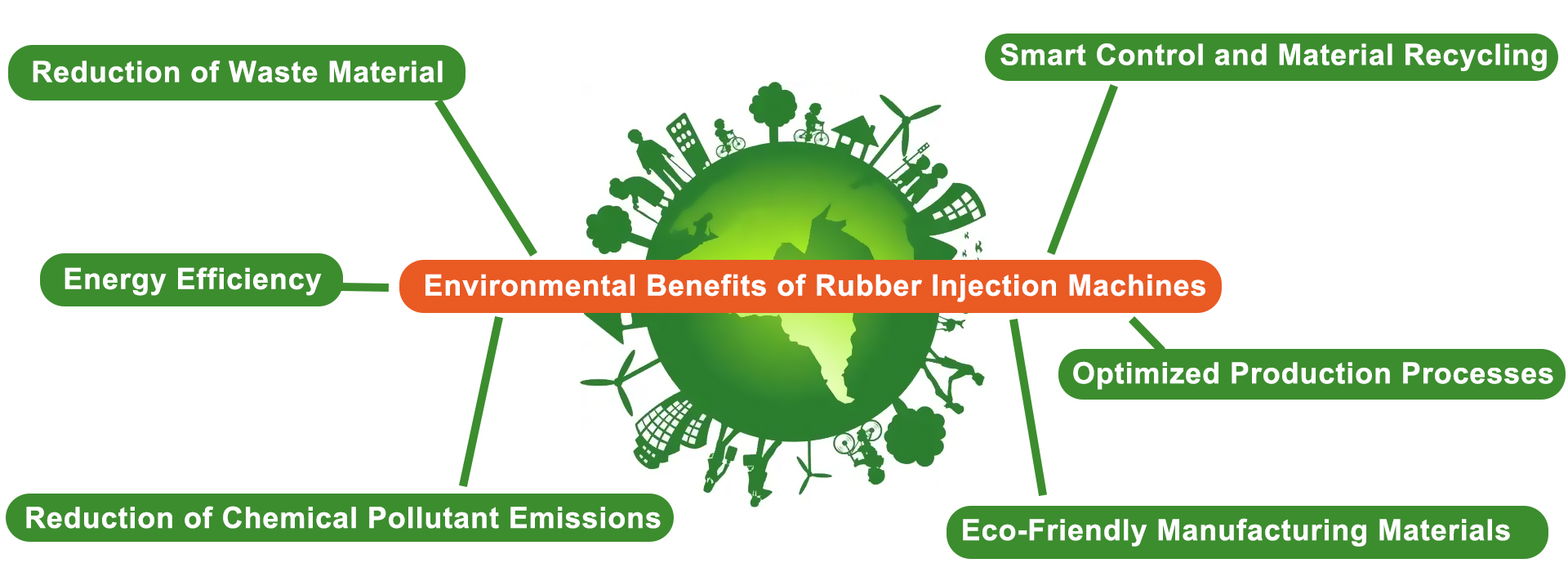
1. Environmental Benefits of Rubber Injection Machines
A rubber injection molding machine is widely used in the production of rubber products. It works by injecting high-temperature molten rubber into molds, precisely shaping and cooling it into the desired form. Compared to traditional rubber compression molding techniques, rubber injection machines offer several key environmental advantages:
1.1 Reduction of Waste Material
In traditional rubber molding processes, excessive material waste often occurs due to imprecise mold operations or overuse of raw materials. In contrast, rubber injection machines allow for precise control of the amount of rubber injected during each cycle, minimizing the excess material used and reducing waste. This not only helps in minimizing material wastage during production but also reduces the costs and environmental impact associated with waste disposal.
1.2 Energy Efficiency
Rubber injection machines are typically equipped with advanced energy control systems that can perform highly efficient operations with reduced energy consumption. By optimizing heating and cooling systems, the machines minimize heat loss and improve energy efficiency. This results in lower electricity consumption, contributing to reduced carbon emissions and a smaller environmental footprint.
1.3 Reduction of Chemical Pollutant Emissions
Traditional rubber processing often involves the use of numerous chemical additives (such as vulcanizing agents and accelerators), which can release volatile organic compounds (VOCs) or other pollutants into the environment during production. Modern rubber injection machines are designed to work with more eco-friendly raw materials and auxiliary agents, significantly reducing the release of chemical pollutants. This not only meets increasingly stringent environmental regulations but also promotes more sustainable production practices.
2. Green Technologies and Environmental Measures
To further enhance the environmental performance of rubber injection machines, many manufacturers have started implementing a range of green technologies and practices. These measures not only improve the eco-friendliness of the equipment but also help businesses reduce overall production costs.
2.1 Smart Control and Material Recycling
Modern rubber injection machines are increasingly adopting intelligent control systems. By integrating advanced sensors, data acquisition systems, and artificial intelligence, these machines can monitor various parameters such as temperature, pressure, and flow rate in real time, ensuring the production process remains optimized. The application of smart control systems not only increases production precision and efficiency but also helps optimize material usage, reducing waste.
In addition, some rubber injection machines are equipped with material recycling systems that allow production scraps to be collected and reused. This approach significantly reduces resource waste and minimizes the environmental impact of waste disposal.
2.2 Eco-Friendly Manufacturing Materials
To support sustainable production, many rubber injection machine manufacturers are promoting the use of recycled rubber and environmentally friendly additives. Recycled rubber offers better recovery potential and lower environmental impact, making it a more sustainable choice for businesses. The use of eco-friendly additives, which replace traditional chemical agents, helps reduce the release of harmful gases and wastewater, further lowering the environmental burden.
2.3 Optimized Production Processes
Optimizing the rubber injection molding process not only boosts production efficiency but also helps reduce energy consumption. For example, improving mold design and heating systems can shorten both heating and cooling times, improving energy efficiency and reducing overall production cycles. Furthermore, the adoption of mold-less or pollution-free processing techniques, which reduce external environmental impacts, is another green manufacturing practice gaining traction in the industry.
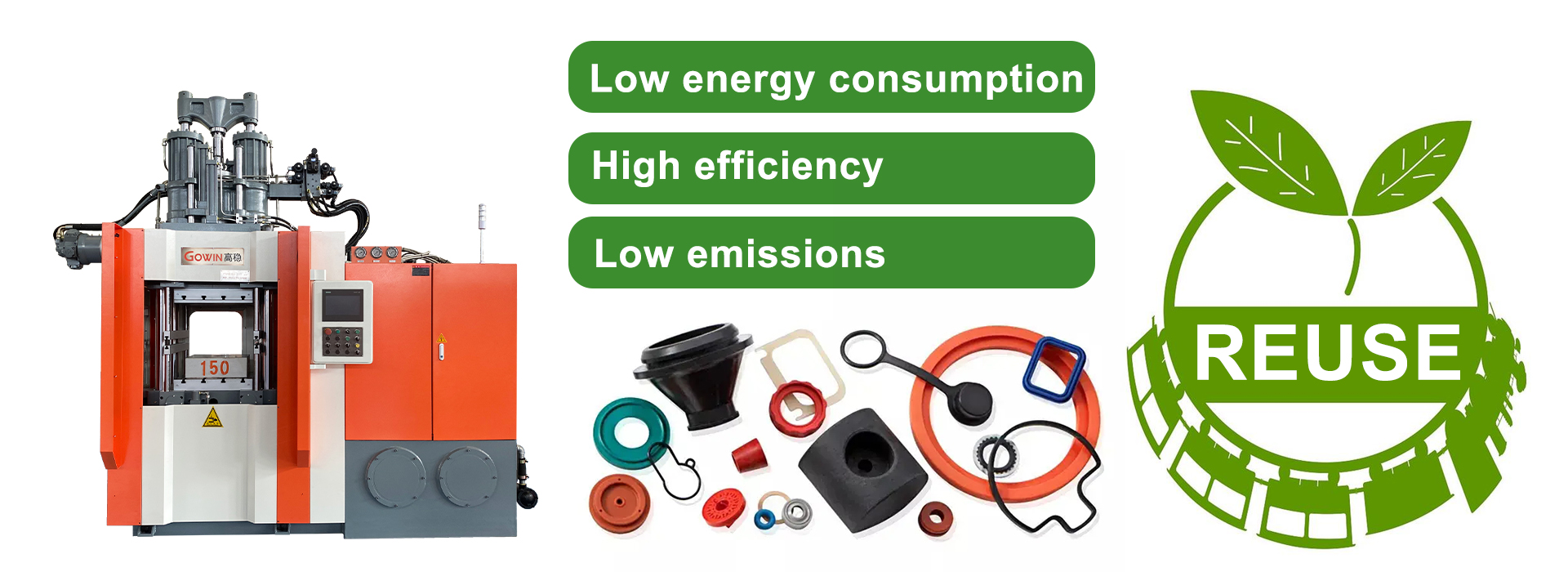
3. The Future of Rubber Injection Machines: Green Technologies and Innovation
As environmental regulations become more stringent and the demand for sustainable products increases, the technological innovation in rubber injection machines will focus even more on low energy consumption, high efficiency, and low emissions.
Some leading rubber injection machine manufacturers are already researching and developing “zero-emission” technologies that aim to further reduce energy consumption and harmful emissions through more precise temperature control systems and smart production processes. Additionally, with the increasing use of Internet of Things (IoT) technologies, rubber injection machines can be remotely monitored and undergo predictive maintenance, further enhancing their sustainability and environmental performance.
4. Conclusion
As environmental requirements become more stringent, the rubber industry faces significant challenges, but also exciting opportunities. Rubber injection machines, as a crucial piece of equipment in rubber processing, have shown considerable potential in driving the green transformation of the industry. By implementing energy-saving, waste-reducing, smart control, and eco-friendly material technologies, these machines not only improve production efficiency but also contribute positively to environmental protection.
For businesses considering purchasing rubber injection machines, choosing equipment with advanced eco-friendly designs and energy-efficient technologies is a critical step toward promoting green manufacturing and meeting environmental standards. Looking ahead, environmental protection will continue to be a driving force for the rubber industry, and rubber injection machines will play a key role in this sustainable evolution.
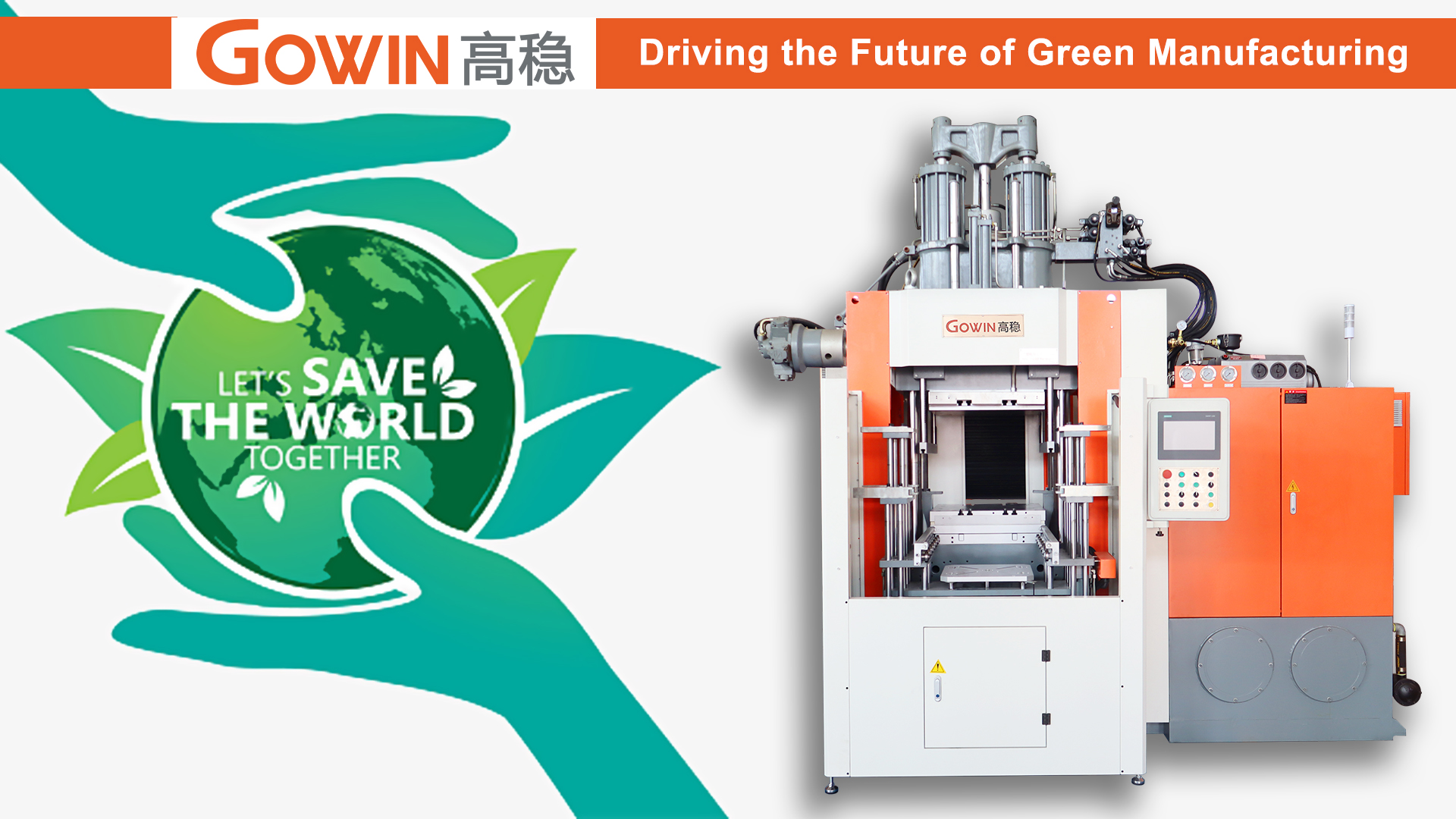
Post time: Dec-06-2024