Introduction to Rubber Injection Machine
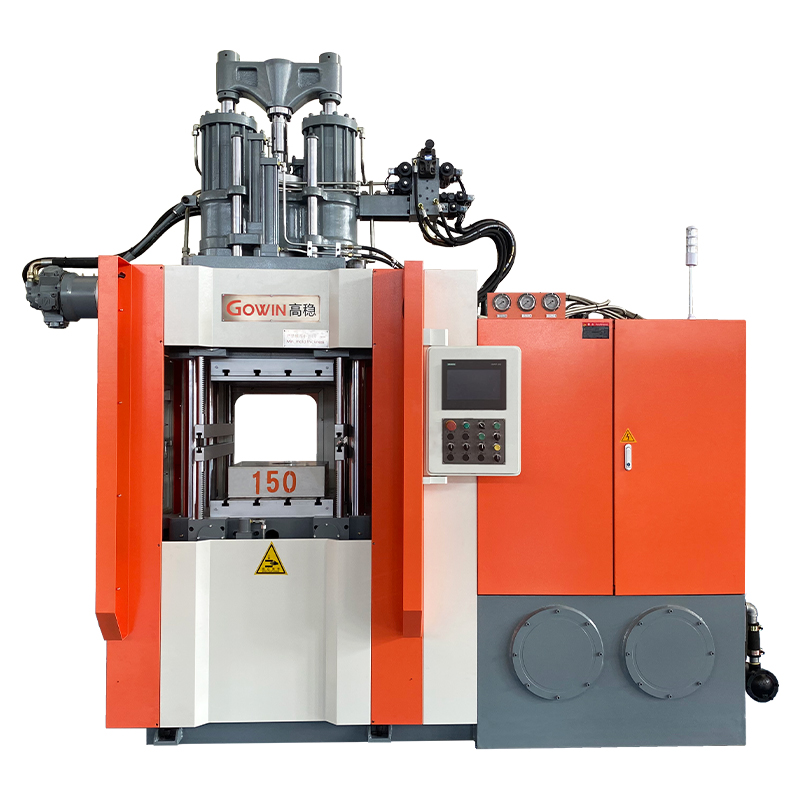
Rubber injection machines play a crucial role in numerous industries due to their unique capabilities and advantages. These machines are essential for the production of high-quality rubber products with precision and efficiency.
In the automotive industry, rubber injection machines are used to manufacture various components such as seals, gaskets, and hoses. The high-pressure and high-precision injection capabilities ensure that these parts meet the strict quality standards required for vehicle performance and safety. For example, the seals produced by rubber injection machines provide a tight fit, preventing leaks and ensuring the proper functioning of engines and other mechanical systems.
In the healthcare industry, rubber injection machines are utilized in the production of medical devices and supplies. Components such as rubber stoppers for vials and syringes are made with precision using these machines. The strict quality control and hygienic production processes ensured by rubber injection machines are essential for medical applications.
The modular-design and multiple-combinations solution of rubber injection machines allow for flexibility in production. Manufacturers can customize the machines to meet specific production requirements, enabling them to produce a wide range of rubber products. This adaptability is particularly valuable in industries where product diversity is essential.
The low-bed and optimized structure of rubber injection machines provide stability and ease of operation. This design feature reduces the risk of accidents and makes maintenance and troubleshooting more accessible. Additionally, the humanized operating system makes it easier for operators to control the machine, reducing the learning curve and increasing productivity.
Key Features and Technologies
(1)Fixed-Cylinder Vertical Injection
Fixed-cylinder vertical injection in rubber injection machines refers to a design where the cylinder remains in a fixed position and the injection process occurs vertically. This concept offers several advantages.
(2)High-pressure & High-precision Injection
High-pressure and high-precision injection is crucial for ensuring quality and efficiency in production. The high pressure enables the rubber material to be forced into the mold with great force, resulting in detailed and accurate replication of the mold's design. This leads to products with smooth surfaces and tight tolerances.
(3)Modular-design & Multiple-combinations Solution
The modular design and multiple-combinations solution of rubber injection machines offer significant benefits for customization and flexibility. Modular design allows manufacturers to easily add or remove components as needed, enabling them to adapt the machine to different production requirements.
(4)Low-bed & Optimized Structure
The low-bed and optimized structure of rubber injection machines provide several advantages in terms of stability and space utilization. The low bed design offers increased stability, reducing the risk of vibrations and ensuring smooth operation.
(5)Humanized Operating System
The humanized operating system of rubber injection machines emphasizes the user-friendly nature for ease of use. With features such as intuitive interfaces and clear instructions, operators can quickly learn and operate the machine.
(6)High-efficiency & High-stability Hydraulic System
The high-efficiency and high-stability hydraulic system plays a crucial role in contributing to reliable operation. The high-efficiency aspect ensures that the machine operates with minimal energy consumption, reducing production costs.
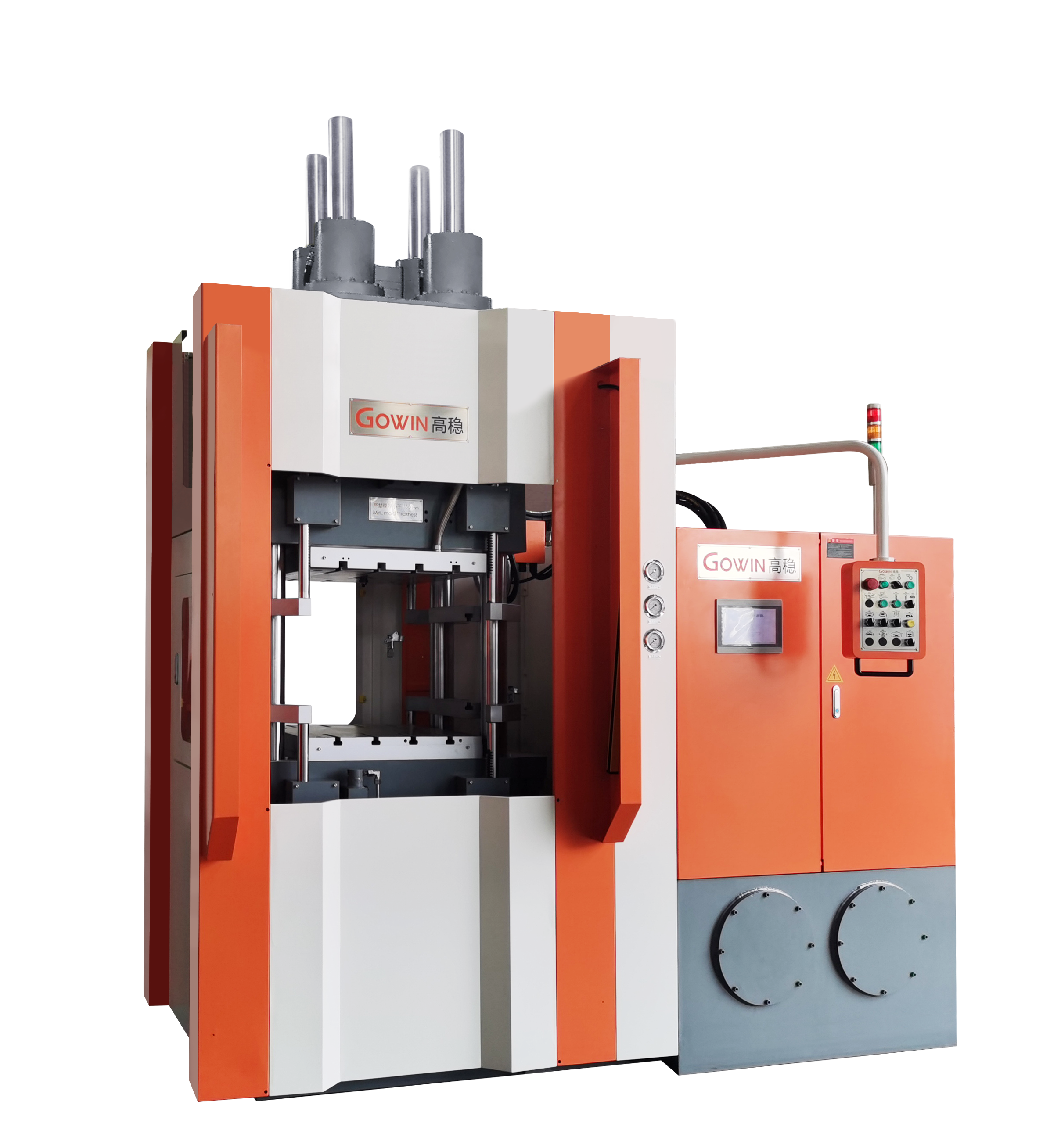
Conclusion
Rubber injection machines with their advanced features play a vital role in modern manufacturing. The fixed-cylinder vertical injection provides stability and efficient material flow, ensuring accurate mold filling. High-pressure and high-precision injection not only results in high-quality products but also increases production efficiency by up to 30% compared to traditional methods. The modular-design and multiple-combinations solution offer customization and flexibility, enabling manufacturers to adapt to diverse product requirements. The low-bed and optimized structure enhance stability and space utilization, making it possible to install the machine in smaller areas. The humanized operating system simplifies operation and reduces operator errors, while the high-efficiency and high-stability hydraulic system reduces costs and ensures consistent performance.
Looking to the future, these advanced features hold great potential. As industries continue to demand more precise and diverse rubber products, rubber injection machines will need to evolve. Technological advancements are likely to further improve the precision and efficiency of these machines. For example, the development of more advanced control systems could enhance the accuracy of high-pressure injection and optimize the modular design for even greater flexibility. Additionally, research into new materials and manufacturing processes may lead to innovations in rubber injection technology.
In conclusion, rubber injection machines with their advanced features are essential for the production of high-quality rubber products. Their potential for future development makes them a key investment for manufacturers looking to stay competitive in an ever-changing market.
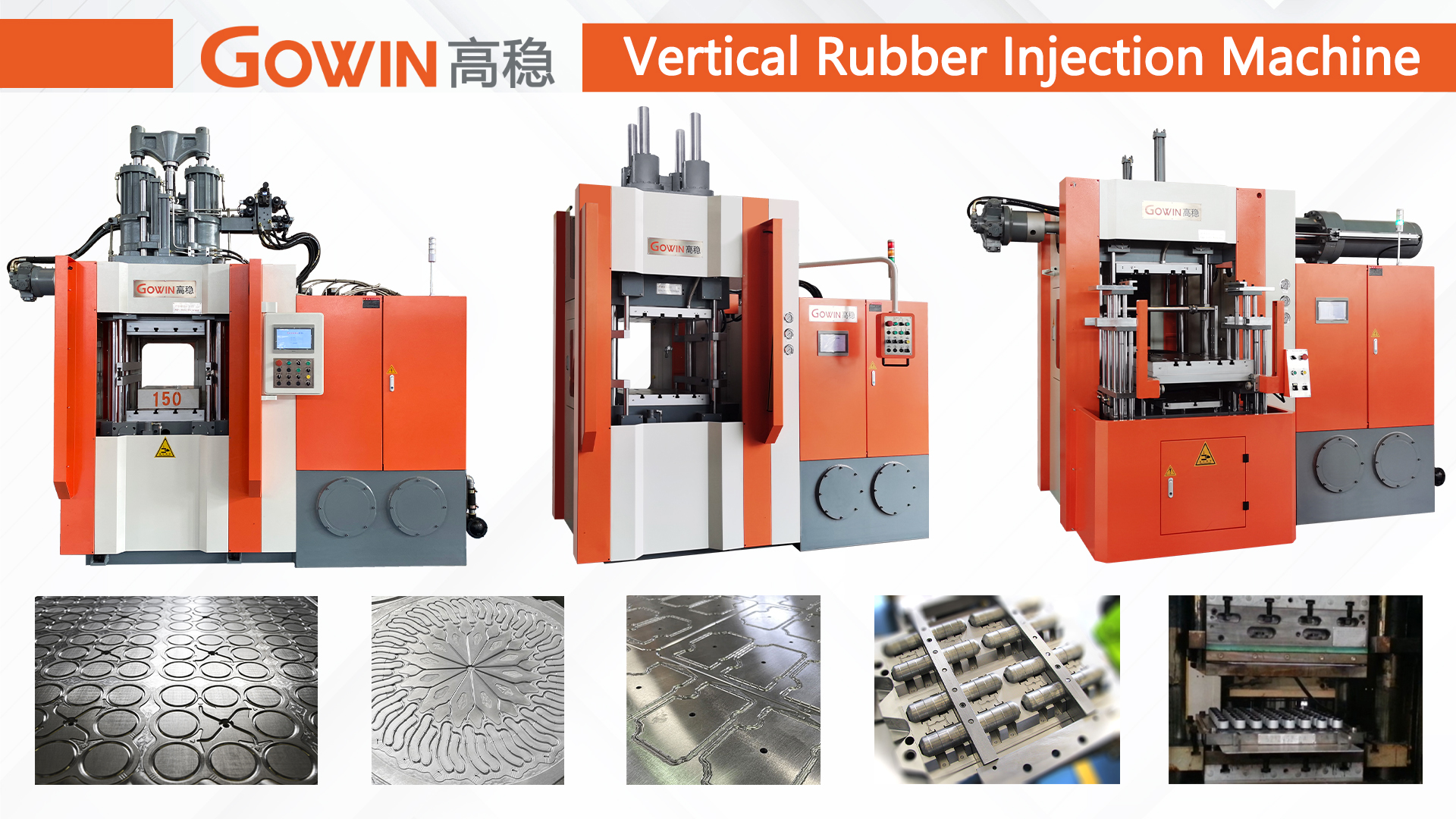
Post time: Oct-25-2024