The combination of rubber injection machine and 3D printing technology is mainly reflected in optimizing mold design, improving production efficiency and realizing more flexible production methods through 3D printing technology. This combination brings many new possibilities to the traditional rubber injection molding process, which is reflected in the following aspects:
① Manufacturing of 3D printing molds
② Optimization of mold cooling system
③ Combination of additive manufacturing and injection molding
④ Optimize injection machine parts
⑤ Reduce material waste and improve environmental protection
⑥ The combination with intelligent manufacturing

1. Manufacture of 3D printing molds
Traditional rubber injection molding usually relies on metal molds, which are costly to manufacture, have long production cycles, and are difficult to modify once the design is complete. With 3D printing technology, manufacturers can quickly print complex molds or mold parts as needed. Specifically, 3D printing can complete the prototyping and iteration of the mold in a short time, which is especially suitable for small batch customization or rapid prototyping.
Advantages:
Fast design and modification: 3D printing can quickly realize mold design changes and test different design schemes.
Cost reduction: Traditional mold manufacturing requires high cost milling and machining, while 3D printing can greatly reduce the initial mold investment, especially for small batch production or custom production.
Realization of complex structure: 3D printing can make complex geometric shapes that can not be realized by traditional processing technology, such as fine cooling channels, complex inner cavity structure, etc., to optimize the performance and production efficiency of the mold.
2. Optimization of mold cooling system
In the process of rubber injection molding, the temperature control of the mold is very important to the production efficiency and product quality. With 3D printing, more efficient cooling systems can be designed and printed to improve heat exchange efficiency and reduce production cycles. Traditional cooling channels are often standardized and simple, while 3D printing technology can optimize the design of cooling channels according to the mold shape, making cooling more uniform and efficient.
Advantages:
Improved thermal management efficiency: More sophisticated and complex cooling channel design optimizes heat distribution and reduces defects caused by uneven rubber cooling.
Reduced cycle time: More efficient cooling designs can significantly reduce production cycles and increase production efficiency.
3. Combination of additive manufacturing and injection molding
In the rubber injection molding process, the injection machine will melt the rubber into the mold, waiting for cooling and curing after taking out the finished product. By combining with 3D printing technology, injection molding can achieve more customized functions, such as printing rubber products with different hardness, different shapes or complex structures according to specific needs. Especially in the production of customized rubber parts, 3D printing can flexibly respond to different customer needs.
Advantages:
Highly customized: 3D printing can print molds or parts with different shapes and designs according to the needs of each order, which improves the product customization ability.
Small batch production: 3D printing does not require a large number of production lines or complex equipment, and can produce small batch and diversified products efficiently and at low cost.
4. Optimize injection machine parts
3D printing can also be used to manufacture and optimize parts of the rubber injection machine itself. For example, the screw, nozzle, heater, controller and other parts of the injection machine, the use of 3D printing technology can produce more customized parts that meet the requirements. This not only helps to improve the efficiency of the injection machine, but also reduces the maintenance cost of components.
Advantages:
Parts customization: Parts with specific functions can be printed for different types of rubber injection machines.
Reduce production downtime: 3D printed parts quickly replace damaged or worn parts, reducing equipment downtime.
5. Reduce material waste and improve environmental protection
3D printing technology has the characteristics of additive manufacturing, in which materials are added layer by layer, rather than requiring the cutting or milling of large amounts of raw materials like traditional manufacturing methods. Therefore, 3D printing can help reduce unnecessary material waste in the production process and improve the efficiency of resource utilization. This is especially important for the rubber molding industry, because in traditional mold manufacturing, a large amount of waste can be generated.
Advantages:
Reduce material waste: 3D printing precisely controls the use of materials, helping to save costs and reduce waste.
Environmental protection: reduce waste and energy consumption, improve the environmental protection of production.
6. Combination with intelligent manufacturing
The combination of 3D printing and intelligent manufacturing technology can make the rubber injection molding process more intelligent and automated. For example, sensors and intelligent control systems are used to monitor parameters such as temperature and pressure of 3D printing molds in real time, thereby optimizing the production process. This combination of technologies can improve production efficiency, reduce manual intervention, and improve production consistency and stability.
Advantages:
Intelligent monitoring: Through the combination of 3D printing technology, real-time monitoring and adjustment of the production process can be realized, and the stability of product quality can be improved.
Automated production: Intelligent manufacturing systems can be combined with 3D printing technology to achieve automated and efficient rubber injection molding production lines.
conclusion
The combination of rubber injection machines and 3D printing technology has brought about a revolution in the manufacturing process. 3D printing can not only optimize mold design and improve production efficiency, but also reduce costs, improve customization capabilities and environmental protection. With the continuous advancement of technology, there may be more innovative production models in the rubber injection molding industry in the future, which will promote the development of the entire manufacturing industry in a more efficient and flexible direction. This combination is not only essential for small-batch, customized production, but also has the potential to play a huge role in large-scale production.
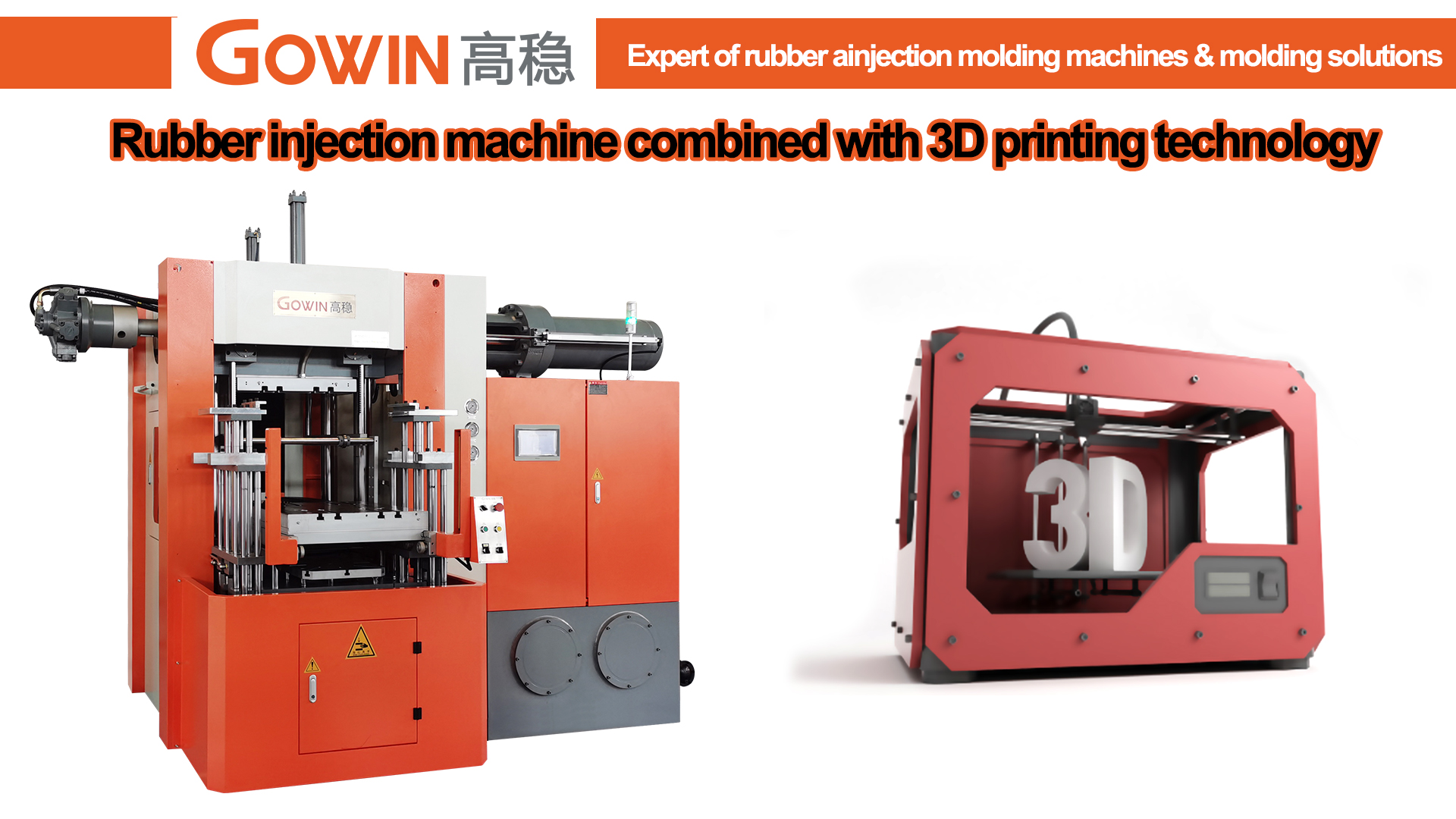
Post time: Dec-13-2024