Introduction
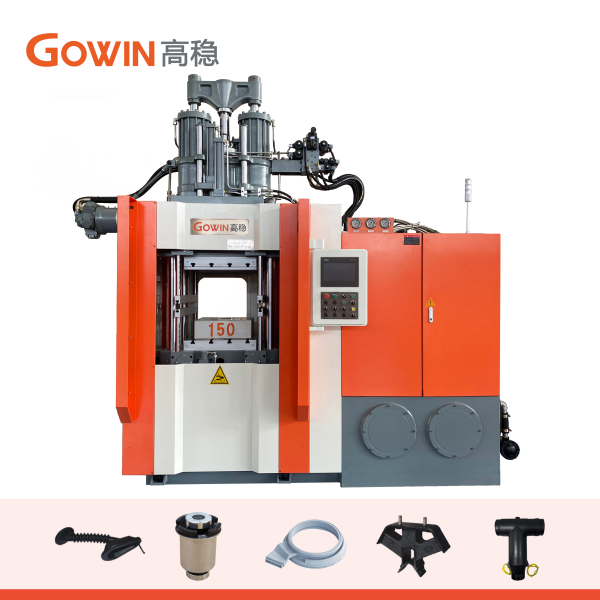
Plastic and rubber injection molding occupies a vital position in modern manufacturing industry. Whether it is common plastic products in daily life, or rubber products widely used in the industrial field, injection molding technology plays a key role. This article aims to delve into the differences between plastic and rubber injection molding to help readers better understand these two important manufacturing processes.
Plastic injection molding is a process in which molten plastic is injected into a mold, which is cooled and solidified to form a specific shape product. According to statistics, the number of plastic products produced by plastic injection molding in the world is huge every year. For example, many plastic items used by car manufacturers, such as interior parts, bumpers, etc., are manufactured by plastic injection molding.
Rubber injection molding is to inject rubber materials into the mold, after vulcanization and other processes, to make a variety of rubber products. Rubber products are also widely used in automotive, machinery, electronics and other fields. For example, automobile tires, seals, etc., are typical products of rubber injection molding.
The importance of the two injection molding processes is not only that they can efficiently produce products with complex shapes, but also that they can ensure the accuracy and quality of the products. By precisely controlling parameters such as temperature, pressure and time during injection, products with high dimensional accuracy and good surface quality can be produced. At the same time, these two processes also have the advantages of high production efficiency and low cost, and can meet the needs of large-scale production.
Overview of plastic injection molding
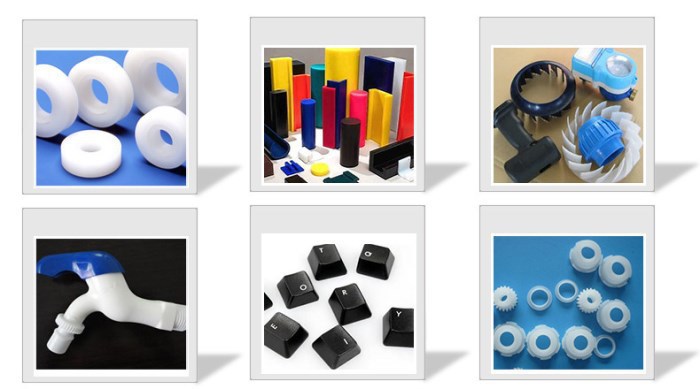
(1) process principle and flow
The process principle of plastic injection molding is to add granular or powdered plastic raw materials to the hopper of the injection machine, the raw materials are heated and melted in a flowing state, driven by the screw or piston of the injection machine, through the nozzle and the pouring system of the mold into the mold cavity, and cooled and solidified in the mold cavity.
The specific process mainly includes the following steps: First, raw material preparation, according to product requirements to choose the appropriate plastic raw materials, such as common polystyrene, polyethylene, polypropylene and so on. These raw materials usually have different performance characteristics, such as strength, toughness, heat resistance, etc., to meet the needs of different products. Then the raw material is added to the injection machine for heating and melting, in this process, it is necessary to strictly control the heating temperature, in general, different plastic raw materials have different melting temperature ranges. For example, the melting temperature of polyethylene is usually between 120 ° C -140 ° C, while the melting temperature of polystyrene is about 180 ° C -220 ° C.
When the raw material is melted and flowing, it is pushed by the screw or piston of the injection machine into the mold cavity through the nozzle and the pouring system of the mold. In this process, the injection pressure is a key parameter, which needs to be large enough to overcome the resistance of the melt during the flow and ensure that the melt can fill the mold cavity. In general, the injection pressure can be between tens to hundreds of mpa.
Finally, in the cooling stage, the plastic is cooled and solidified in the mold cavity through the cooling system of the mold. The length of the cooling time depends on the type of plastic, the thickness of the product and other factors. Generally speaking, the cooling time of thinner products is shorter, which may be between tens of seconds and a few minutes; The cooling time of thicker products will be extended accordingly.
(2) Characteristics and advantages
Plastic injection molding has many characteristics and advantages. First, it can make complex shapes. Because the plastic has good fluidity in the molten state, it can be filled with complex shape mold cavities, so as to produce plastic products with various complex shapes, such as products with internal cavities and reverse structures.
Secondly, the precision is higher. By precisely controlling parameters such as temperature, pressure and time during the injection process, products with high dimensional accuracy can be produced, and dimensional tolerances can be controlled between a few to dozens of wires. For example, some precision electronic product shells can achieve high dimensional accuracy requirements through plastic injection molding.
In addition, plastic injection molds are diverse, suitable for a variety of processing trade forms. Different injection molds can be designed for different products according to their shape, size and performance requirements. Moreover, injection molds can be mass-produced, with high production efficiency, and are suitable for various forms of processing trade, such as OEM (original equipment manufacturer) and ODM (original design manufacturer).
At the same time, plastic injection molding has a wide range of adaptation. It can be used to produce a variety of plastic products, from daily necessities such as tableware, toys, to industrial products such as electrical enclosures, auto parts and so on. According to statistics, about 70% of the world's plastic products are produced by injection molding.
Overview of rubber injection molding machine
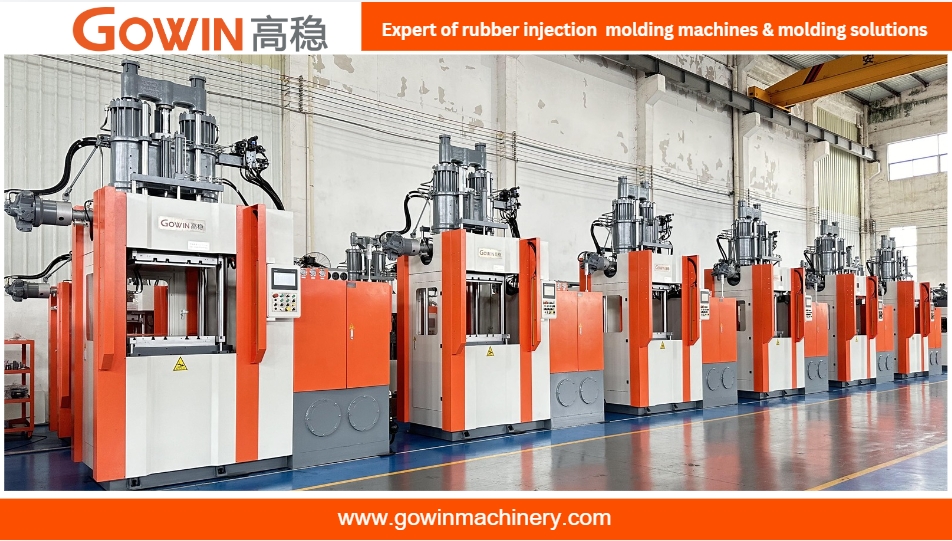
(1) process principle and flow
Rubber injection molding Machine is a kind of processing technology that sends materials into the forming mold through a high-performance rubber extruder, and after a certain pressure and temperature, the rubber raw materials form the required shape and size in the mold.
The specific process is as follows:
Preparatory work: including rubber raw material screening, drying, preheating and other operations, as well as mold design, manufacturing and debugging. The screening of rubber raw materials is crucial to ensure that the quality and performance of raw materials meet the requirements of products. For example, for some high-performance rubber products, such as automobile tires, seals, etc., it is necessary to choose high-quality rubber raw materials to ensure the strength, wear resistance and aging resistance of the products. In the drying and preheating process, the temperature and time should be strictly controlled to avoid excessive drying or insufficient preheating of rubber raw materials. The design and manufacture of the mold needs to be carefully designed according to the shape, size and performance requirements of the product to ensure the accuracy and quality of the mold.
Material production: The dry rubber particles are added to the rubber extruder, and the material is pre-treated by a series of processes such as heating and extrusion. In this process, the performance and parameter Settings of the rubber extruder are very critical. For example, the temperature of the extruder, screw speed and other parameters will directly affect the plasticizing effect and quality of the rubber material. Generally speaking, the temperature of the extruder can be between 100 ° C and 150 ° C, and the screw speed can be between tens to hundreds of revolutions per minute, and the specific parameters should be adjusted according to the type and performance requirements of the rubber material.
Molding: The pre-treated rubber material is fed into the mold by the injection machine for the molding process. At this time, a certain pressure and temperature need to be connected to make the rubber raw material form the product of the desired shape and size. The pressure and temperature in the molding process are key parameters, the pressure can generally be between tens to hundreds of mpa, and the temperature can be between 150 ° C and 200 ° C. Different rubber products have different requirements for pressure and temperature, for example, for some large rubber products, such as rubber drum screens, bridge shock absorbers, etc., higher pressure and temperature are needed to ensure the molding quality of the products.
Compression demoulding: After the molding is completed, it is necessary to cool down and demoulding to remove the rubber products from the mold. The cooling process should be carried out slowly to avoid deformation or cracking of products due to rapid temperature change. Be careful when demoulding to avoid damaging the product.
(2) Characteristics and advantages
Single production capacity: the single production capacity of rubber injection molding machine is generally between tens of grams and several kilograms, which greatly improves the output of finished products.
High product accuracy: The rubber injection molding machine can precisely control the temperature, pressure and other parameters of the material during the molding process, thus greatly improving the accuracy of the product.
Short molding cycle: Because rubber injection molding can form multiple products at the same time, and the production capacity is large, the molding cycle is relatively short. For example, in the production of some auto parts, the use of rubber injection molding process can greatly improve production efficiency and shorten the production cycle.
High quality of the finished product: rubber injection molding can reduce the product because of uneven forming, bubbles and other problems, so that the product quality is greatly improved. For example, the automotive seals produced by rubber injection molding process have good sealing and wear resistance, which can effectively improve the performance and service life of automobiles.
The difference between plastic and rubber injection molding
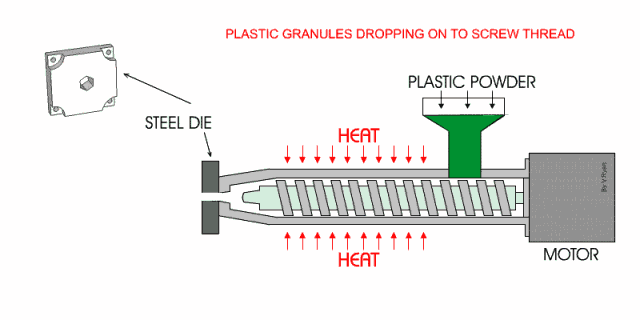
(1) Differences in raw material characteristics
The raw material of plastic is usually thermoplastic or thermosetting resin, which has high hardness and rigidity, and different plastic raw materials have different performance characteristics, such as strength, toughness, heat resistance and so on. For example, polyethylene has good chemical resistance and electrical insulation, but its strength and heat resistance are relatively low; Polystyrene has high transparency and hardness, but it is brittle. These characteristics determine that the plastic requires a specific temperature and pressure range during injection molding to ensure that the raw material can fully melt and fill the mold cavity.
The raw material of rubber is natural rubber or synthetic rubber, which has high elasticity and flexibility. Rubber is usually soft and easy to deform in the unvulcanized state, while it has higher strength and wear resistance after vulcanization. The elastic properties of rubber make it necessary to take into account the shrinkage rate and resilience of the material in the injection molding process to ensure the dimensional accuracy and shape stability of the product. For example, when designing a mold for rubber products, it is necessary to take into account that the shrinkage rate of rubber is large, usually between 1%-5%, while the shrinkage rate of plastic is generally between 0.5% and 2%.
(2) Differences in process parameters
In terms of temperature, the temperature of plastic injection molding is usually higher, and different plastic raw materials have different melting temperature ranges. For example, the melting temperature of polyethylene is usually between 120 ° C and 140 ° C, and the melting temperature of polystyrene is about 180 ° C and 220 ° C. The temperature of rubber injection molding is relatively low, generally between 100 ° C and 200 ° C, and the specific temperature depends on the type and performance requirements of rubber. For example, the vulcanization temperature of natural rubber is usually between 140 ° C and 160 ° C, and the vulcanization temperature of synthetic rubber may be different.
In terms of pressure, plastic injection molding requires a high injection pressure, generally between tens to hundreds of mpa, to overcome the resistance of the melt in the flow process and ensure that the melt can fill the mold cavity. The pressure of rubber injection molding is relatively low, generally between tens to hundreds of mpa, but for some large rubber products, higher pressure may be required. For example, when producing large rubber products such as rubber drum screens and bridge shock absorbers, high pressure is needed to ensure the molding quality of the products.
(3) Differences in product characteristics
In terms of shape, plastic injection molding can produce a variety of products with complex shapes, such as plastic products with internal cavities, reverse structures, etc. Due to its high elasticity and flexibility, rubber products are usually relatively simple in shape, mostly seals, tires and so on.
In terms of accuracy, plastic injection molding can produce products with high dimensional accuracy, and the dimensional tolerance can be controlled between a few wires and dozens of wires. The accuracy of rubber injection molding products is relatively low, but for some high-performance rubber products, such as automotive seals, etc., it can also achieve higher accuracy requirements.
In terms of use, plastic products are widely used in daily necessities, industrial products and other fields, such as tableware, toys, electrical shell, auto parts and so on. Rubber products are mainly used in automotive, machinery, electronics and other fields, such as tires, seals, shock absorbers and so on.
Conclusion
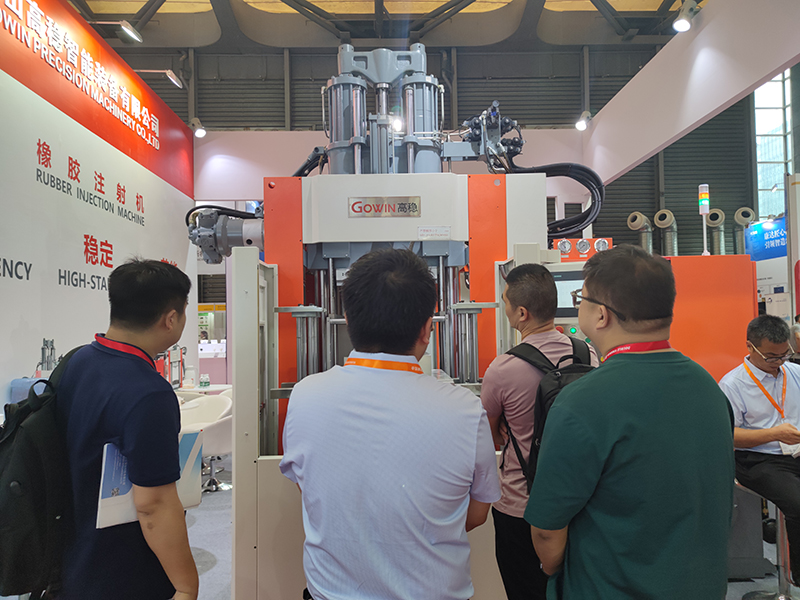
There are obvious differences between plastic and rubber injection molding in raw material characteristics, process parameters and product characteristics.
From the perspective of raw material characteristics, plastic raw materials are usually thermoplastic or thermosetting resins, which have high hardness and rigidity, and different plastics have different properties. The raw material of rubber is natural rubber or synthetic rubber, which has high elasticity and flexibility.
In terms of process parameters, the plastic injection molding temperature is higher, the melting temperature range of different plastics is different, and the injection pressure is higher to ensure that the melt is full of the mold cavity. Rubber injection molding temperature is relatively low, the pressure is also relatively low, but large rubber products may require higher pressure.
Product characteristics, plastic injection molding can manufacture complex shape products, high precision, widely used in daily life and industrial fields. Due to high elasticity, rubber products are usually relatively simple in shape and relatively low in accuracy, but high-performance rubber products can also meet high precision requirements, mainly used in automotive, machinery, electronics and other fields.
These two injection molding processes are critical to related industries. In the plastic products industry, plastic injection molding is efficient, low cost, can meet the needs of large-scale production, and provides a rich variety of products for various fields. In the rubber products industry, the single production capacity of rubber injection molding is large, the product precision is high, the molding cycle is short, and the finished product is high quality, which provides key parts and seals and other products for the automobile, machinery and other industries, ensuring the stable development of these industries. In short, plastic and rubber injection molding plays an irreplaceable role in modern manufacturing, and their respective characteristics and advantages also provide strong support for the development of different industries.
Post time: Nov-08-2024