As global railway infrastructure expands—driven by high-speed rail (HSR) projects, metro modernization, and sustainability mandates—the demand for precision-engineered anti-vibration rubber parts has surged. These components, critical for passenger comfort, track stability, and noise reduction, require advanced manufacturing solutions to meet stringent technical standards and production scalability. Enter the Gowin GW-R400L Vertical Rubber Injection Machine—a game-changer designed to address these challenges while delivering unmatched efficiency, energy savings, and quality.
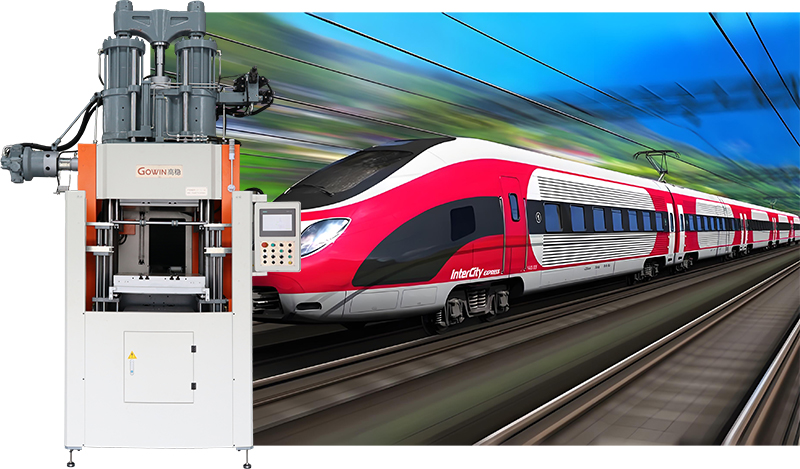
1. Industry Trends: The Rise of Railway Rubber Components
- High-Speed Rail: Projects like China’s Fuxing HSR and the UK’s HS2 demand rubber parts capable of withstanding extreme loads and dynamic stresses .
- Sustainability: Rubber components must now incorporate eco-friendly materials (e.g., recycled rubber) and energy-efficient production processes to align with global decarbonization goals.
- Smart Manufacturing: The integration of IoT sensors in rubber parts for real-time vibration monitoring is reshaping production requirements .
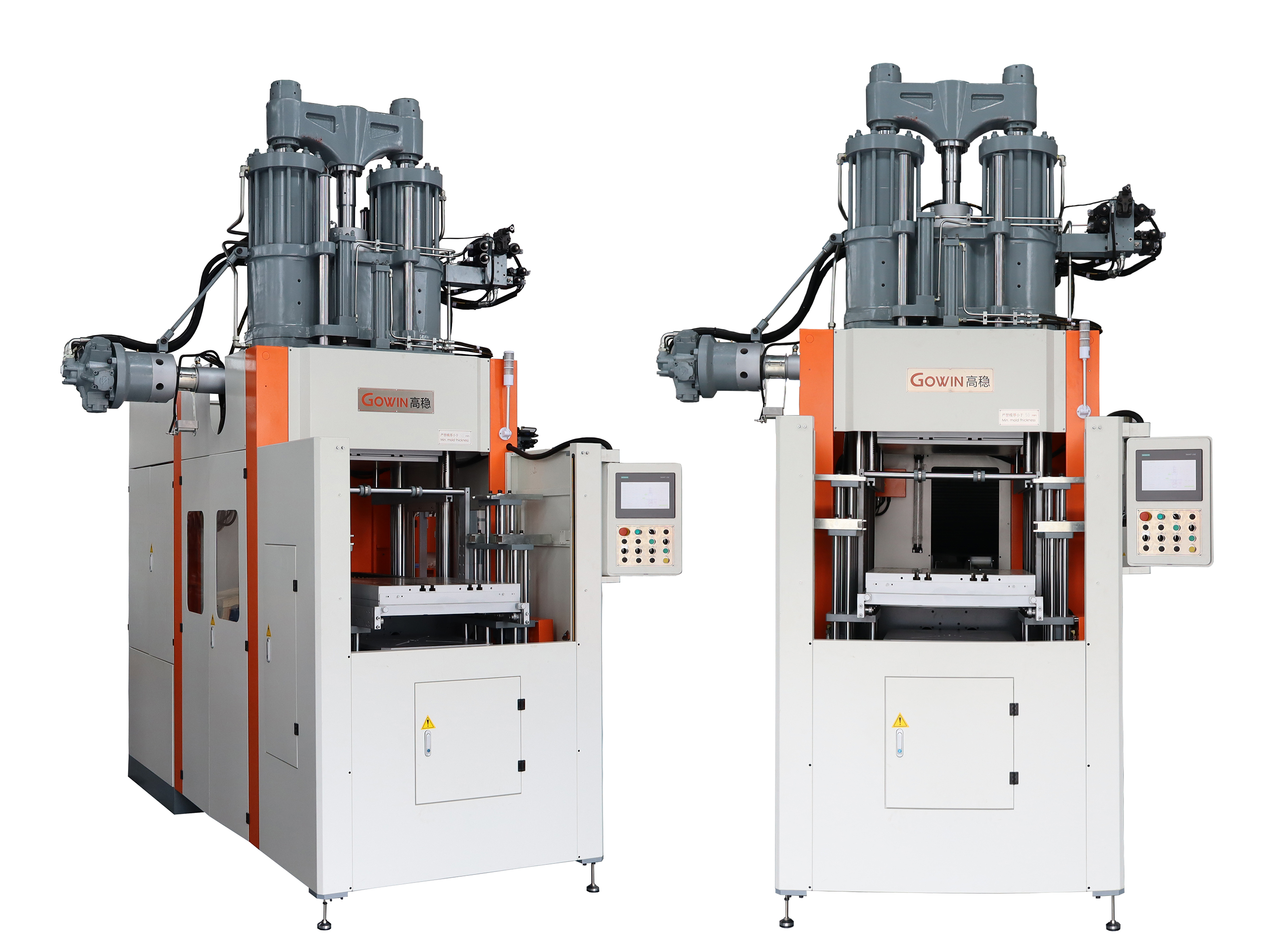
2. Gowin GW-R400L: Engineered for Railway Excellence
The GW-R400L is tailored to tackle these challenges with precision and power:
Key Features & Benefits
400T Clamping Force: Enables large-scale production of high-load components like bridge bearings (e.g., 3,000-ton capacity rubber bearings for projects like the Hong Kong-Zhuhai-Macao Bridge ).
8,000cc Injection Volume: Handles thick-walled parts and multi-cavity molds, reducing cycle times by up to 30% compared to traditional machines.
4RT Ejecting System: Ensures consistent part removal for complex geometries, minimizing defects and waste.
High-Performance Servo System: Achieves 35–80% energy savings via real-time pressure/flow control, aligning with ISO 50001 energy management standards .
Specialized Sliding System: Reduces friction by 50%, extending machine lifespan and lowering maintenance costs.
Technical Edge
Compliance: Meets international standards like GB/T 36375-2018 (railway rubber springs) and TB/T 3469-2016 (dynamic stiffness requirements) .
Material Flexibility: Supports high-damping rubber compounds, TPEE, and flame-retardant materials for fire-resistant applications .
Precision:Closed loop control system ensures ±0.5% shot weight accuracy, critical for aerospace-grade components.
3. Energy Efficiency: A Competitive Advantage
- Servo-Driven Hydraulics: Unlike traditional hydraulic machines, the GW-R400L adjusts motor speed based on real-time demand, slashing energy consumption. For example, a typical 12-hour production run saves $2,000/month compared to legacy systems .
- Cooling Optimization: Reduced oil temperature fluctuations cut cooling water usage by 50%, further lowering operational costs.
- Certifications: Complies with China’s GB/T 30200-2023 energy efficiency standard, ensuring eligibility for green manufacturing subsidies .
4. Case Study: Transforming Railway Production
- Efficiency: Cycle time reduced from 45 to 32 seconds.
- Quality: Scrap rate dropped from 8% to 1.5%.
- Sustainability: Annual CO₂ emissions decreased by 120 tons.
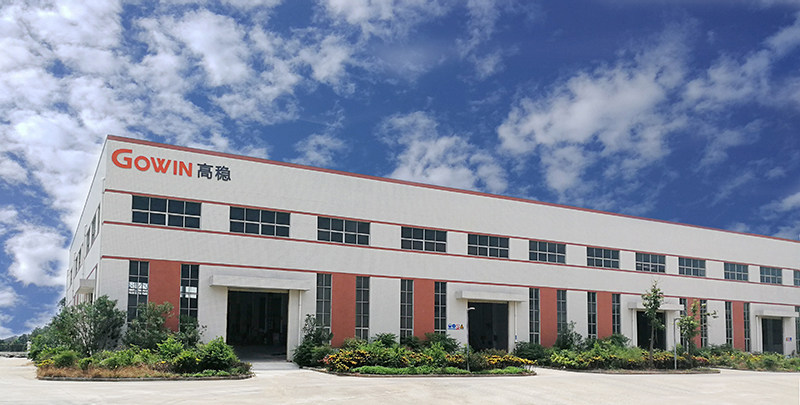
5. Why Choose Gowin?
- Global Support: Gowin’s network of 20+ service centers ensures rapid response times and localized technical expertise.
- Customization: Tailored solutions for niche applications, such as railway noise barriers or vibration-damping pads.
- ROI Focus: Typical payback period of 12–18 months through energy savings and productivity gains.
6. Future-Proof Your Operations
Post time: Apr-08-2025