When choosing a silicone rubber machine that suits your needs, you need to consider various factors comprehensively. Here are some suggestions:
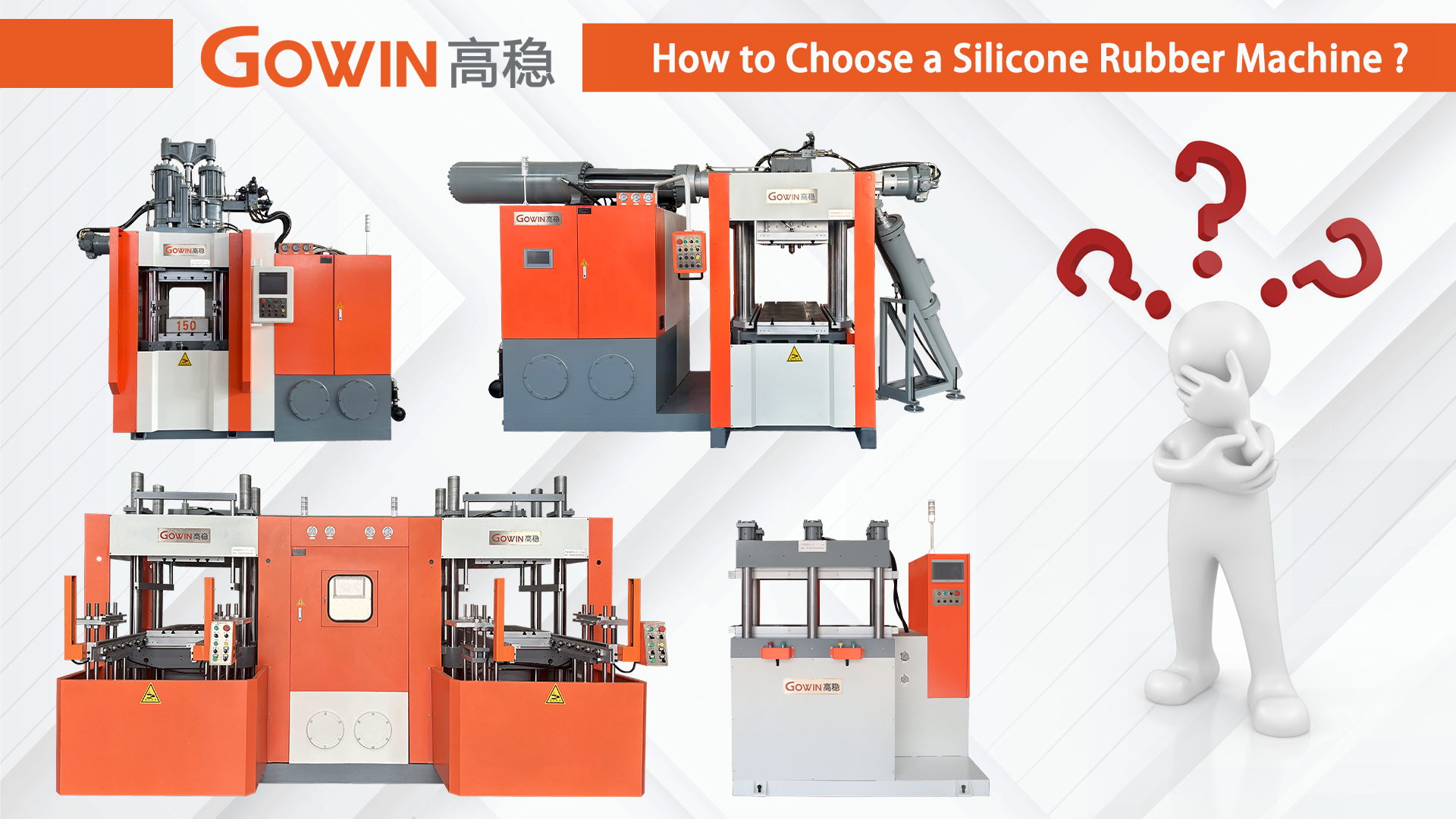
1. **Define production needs**
- **Product type and specification**: Different silicone rubber products have different requirements for machines. For example, for the production of small products such as sealing rings and rubber hoses, a small and precise injection machine may be required; while for the production of large rubber components such as automobile tires and rubber plates, a large-scale forming equipment is needed. Clearly define the product type, size, shape, and precision requirements of the products you want to produce to determine the applicable range of the machine.
- **Production batch**: If it is large-scale mass production, you should choose a machine with high production efficiency and a high degree of automation, such as a fully automatic rubber injection molding machine, which can produce a large number of products quickly and stably; if it is small-batch production or in the research and development trial production stage, you can consider choosing a small, multifunctional, and flexible machine, such as an experimental open mill or a small injection machine, which can not only meet production needs but also reduce costs and floor space.
- **Production process**: Understand your production process, such as the specific requirements of mixing, extrusion, injection, vulcanization and other links. For example, for processes that require high-precision mixing, you should choose a machine with good mixing effects, such as a mixer with a special stirring device or temperature control system; for injection processes, pay attention to whether parameters such as injection pressure, injection speed, and injection volume meet the requirements.
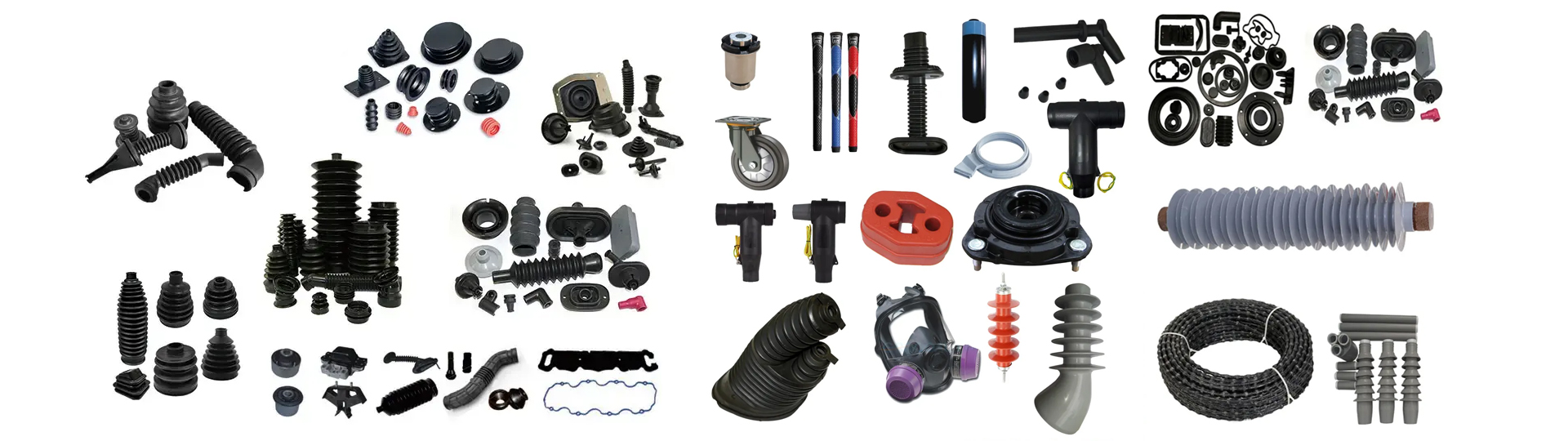
2. **Evaluate machine performance**
- **Processing precision**: Silicone rubber products have high precision requirements, especially for some precision parts. Check the processing precision of the machine, such as dimensional precision, weight precision, surface roughness, etc., to see if it meets the product requirements. For example, for some high-precision rubber seals, the dimensional tolerance may be required to be within a very small range, which requires the machine to have high-precision processing capabilities.
- **Production efficiency**: Determine the required production efficiency according to production needs. Check the machine's parameters, such as the number of injections per minute, extrusion speed, vulcanization time, etc., and calculate the number of products that can be produced in unit time to ensure that the production efficiency of the machine can meet production plans and market demands. At the same time, also consider the stability and reliability of the machine to avoid affecting the production schedule due to frequent failures.
- **Energy consumption**: For machines that operate for a long time, energy consumption is an important cost factor. Understand the machine's power, power consumption, energy utilization efficiency and other indicators. Choosing an energy-saving machine can reduce production costs. For example, some new rubber machines adopt advanced energy-saving technologies such as frequency conversion drive and intelligent temperature control, which can effectively reduce energy consumption.
3. **Consider machine quality and reliability**
- **Brand and reputation**: Choose a silicone rubber machine manufacturer with a well-known brand and a good reputation. You can learn about the reputation and product quality of different brands through industry exhibitions, online forums, and customer evaluations. Well-known brands usually have more experience and stricter standards in technology research and development, production technology, and quality control. Their product quality and after-sales service are more guaranteed.
- **Machine structure and material**: Check whether the machine's structural design is reasonable and sturdy and durable. The materials of key components such as the frame, screw, and mold should have sufficient strength, wear resistance, and corrosion resistance to ensure that the machine can maintain stable performance during long-term use. For example, a screw made of high-quality alloy steel has better wear resistance and anti-deformation ability, which can prolong the service life of the machine.
- **Quality certification and inspection**: Check whether the machine has passed relevant quality certifications, such as ISO quality system certification. Understand whether the manufacturer has a strict quality inspection process and standard, and whether the machine has undergone comprehensive testing and inspection before leaving the factory to ensure that the quality of the machine meets the requirements.
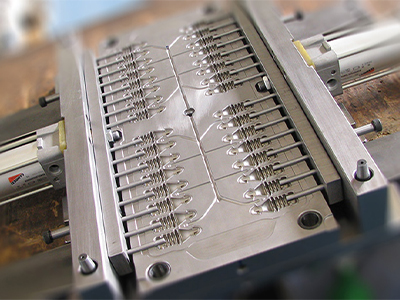

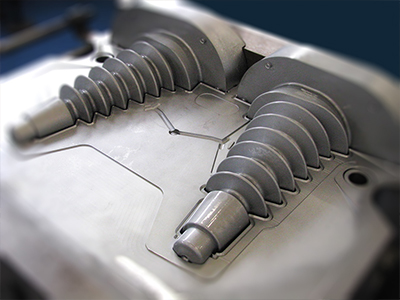
4. **Pay attention to technical support and after-sales service**
- **Technical training**: Whether the manufacturer can provide professional technical training to help operators familiarize themselves with the machine's operation methods, maintenance points, and common fault handling. Good technical training can enable operators to get started quickly, improve production efficiency, and reduce machine failures caused by improper operation.
- **After-sales service network**: Understand the coverage and response speed of the manufacturer's after-sales service network. During the use of the machine, various problems may need to be solved in a timely manner. A manufacturer with a perfect after-sales service network and rapid response can provide technical support, maintenance services, and spare parts supply in a timely manner, minimizing the impact of machine downtime on production.
- **Spare parts supply**: Ensure that the manufacturer can provide spare parts for the machine stably for a long time. Because during the use of the machine, it is inevitable that there will be wear or damage to spare parts. Replacing spare parts in time can ensure the normal operation of the machine. Understand information such as the price and supply cycle of spare parts so that you can obtain the required spare parts in time when needed.
5. **Calculate costs and budget**
- **Machine price**: According to your budget range, choose a machine with a reasonable price. But don't just look at the initial purchase price of the machine. You also need to comprehensively consider factors such as the machine's performance, quality, after-sales service, as well as energy consumption costs, raw material consumption, mold costs, and maintenance costs during long-term use. Conduct a comprehensive cost analysis and choose a machine with high cost performance.
- **Operating cost**: In addition to the price of the machine itself, you also need to consider operating costs, including energy consumption costs, raw material consumption, mold costs, maintenance costs, etc. For example, although some machines have a lower purchase price, they may have higher energy consumption or shorter mold service life, which may lead to an increase in long-term operating costs. Consider these factors comprehensively when choosing.
6. **Inspect supplier strength**
- **Production capacity**: Understand the supplier's production scale, production equipment, production technology, etc., and judge whether it has sufficient ability to provide the required machines on time, with quality and in quantity. A supplier with strong production capacity can ensure the delivery cycle and quality stability of the machine.
- **R & D capability**: Silicone rubber machine technology is constantly developing. Choosing a supplier with strong R & D capabilities can ensure the technological advancement and applicability of the machine. Understand whether the supplier has a professional R & D team, whether it actively invests in R & D funds, and whether there are new products or new technologies launched. This will help you choose a machine that is more in line with future development needs.
- **Industry experience**: The supplier's experience in the silicone rubber industry is also very important. A supplier with rich industry experience has a deeper understanding of industry needs and development trends and can provide more professional advice and solutions to help customers choose the most suitable machine and provide better technical support during the production process.
As for illustrations, you can search for images of silicone rubber machines on stock photo websites like Shutterstock or Pixabay. Some possible images could include different types of rubber injection molding machines, close-ups of machine components, and factory scenes with machines in operation.
Post time: Oct-07-2024