In the world of power transmission and distribution, electrical safety and reliability are paramount. To ensure high-performance and long-lasting equipment, manufacturers rely on high-quality components like silicone insulators and lightning arresters. But have you ever wondered how these essential parts are made? The answer lies in a cutting-edge technology: solid-state silicone injection molding machines.
In this article, we’ll take a closer look at how solid-state silicone injection machines work, and why they are so crucial for producing durable insulators and lightning arresters that protect our electrical infrastructure.
What Is a Solid-State Silicone Injection Machine?
A solid-state silicone injection machine is a specialized piece of equipment used to produce parts made from high-viscosity silicone rubber. Silicone rubber is widely used in the power industry because of its excellent electrical insulation properties, resistance to weathering, and ability to withstand extreme temperatures.
The machine works by heating and injecting solid-state (high-viscosity) silicone into molds, where it cools and solidifies into the desired shape. This process requires precision, as the silicone must flow evenly into the molds and form parts with tight tolerances, ensuring they meet the high standards required for power equipment.
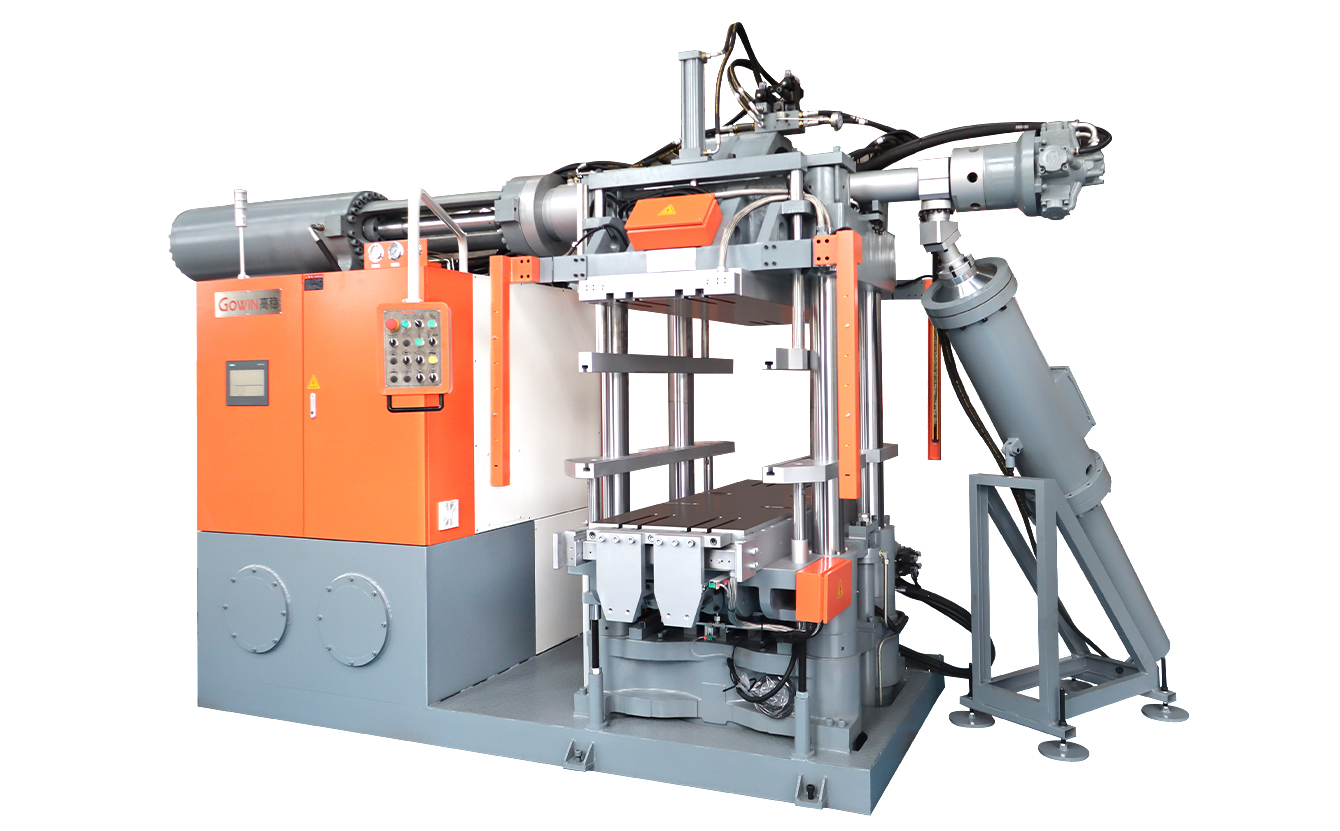
How Do These Machines Work?
1.Material Preparation and Mixing:
Before injection, silicone rubber is mixed with curing agents and other additives to ensure it meets the desired properties, such as electrical insulation and weather resistance.
2.Heating and Extrusion:
The silicone material is then heated to a specific temperature, reducing its viscosity so it can flow easily into molds. The solid-state silicone is extruded through a screw or piston mechanism in the injection machine.
3.Injection into Molds:
The heated silicone is injected into precision molds where it takes the shape of the desired part, such as an insulator or lightning arrester shell. The molding process is crucial because the parts need to have excellent dimensional accuracy for proper function.
4.Curing and Cooling:
Once the silicone is injected into the mold, it undergoes a curing process (heat treatment), which solidifies the material. The curing time and temperature are carefully controlled to ensure optimal performance.
5.Demolding and Inspection:
After cooling, the part is removed from the mold. Quality control tests ensure the final product meets required standards for electrical performance, mechanical strength, and durability.
Why Are Solid-State Silicone Injection Machines Important for the Power Industry?
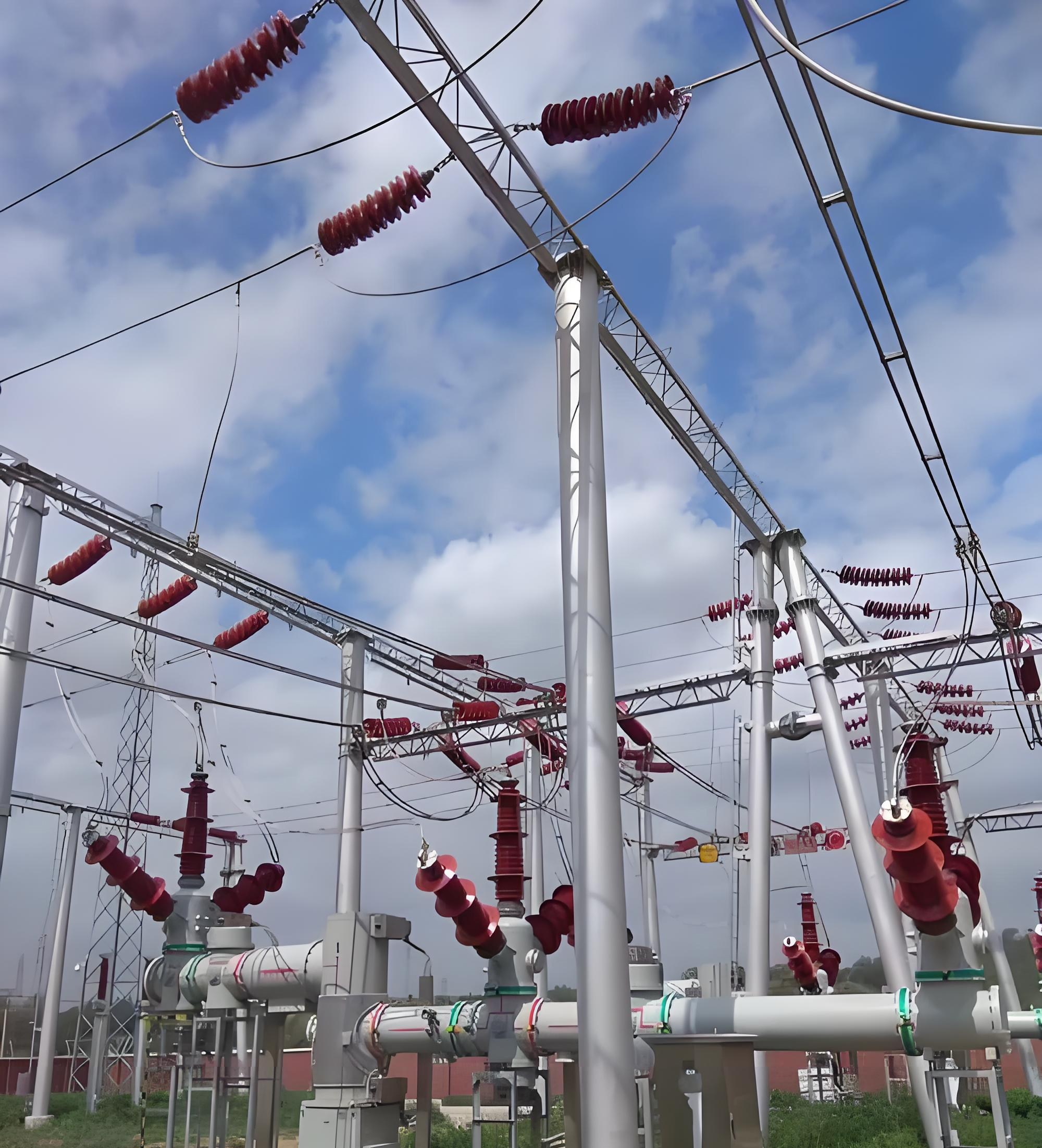
The use of silicone in power transmission equipment like insulators and lightning arresters has become indispensable. Here's why:
Electrical Insulation:
Silicone insulators help maintain the safety and efficiency of power lines by preventing electrical leakage, even in high-voltage conditions. The solid-state silicone injection machine ensures that these insulators are produced with precise electrical insulation properties that can withstand extreme weather conditions and electrical stress.
Weather Resistance:
Power infrastructure must endure all kinds of environmental challenges—extreme heat, heavy rain, snow, and even UV radiation from the sun. Silicone rubber, due to its excellent weathering resistance, is the go-to material for insulating and protecting electrical equipment in outdoor environments. Injection machines guarantee that these properties are embedded in every part produced.
Mechanical Strength and Durability:
Insulators and lightning arresters need to withstand high mechanical stresses (e.g., tension, impact) in addition to electrical stress. Solid-state silicone injection machines ensure that the silicone used has the right balance of strength, flexibility, and durability.
Applications in Insulators and Lightning Arresters
Silicone Insulators:
Used in high-voltage power lines and substations, silicone insulators are essential for preventing electrical leakage and ensuring reliable power transmission. The injection molding process produces insulators with a smooth surface that reduces the risk of contamination buildup and improves their performance over time.
Lightning Arresters:
Lightning arresters protect electrical equipment from the damaging effects of lightning strikes and electrical surges. Silicone rubber is used for the outer casing of these devices due to its non-conductive nature and ability to absorb and dissipate large amounts of electrical energy. Solid-state silicone injection machines produce lightning arrester components that can withstand direct strikes while protecting vital equipment.
The Benefits of Using Solid-State Silicone Injection Machines in the Power Industry
Precision and Consistency:
With automation and precise control of injection parameters (temperature, pressure, speed), manufacturers can ensure each part is produced to exact specifications, improving overall quality and reliability.
Higher Production Efficiency:
The injection molding process is fast and can produce large volumes of parts with minimal waste, which helps reduce production costs and time.
Customization:
Different power equipment requires different shapes, sizes, and performance features. Solid-state silicone injection machines can be easily adapted to create custom molds for various components, from small seals to large insulators.
Energy Efficiency:
Modern injection machines are designed to be energy-efficient, reducing the overall carbon footprint of production processes.
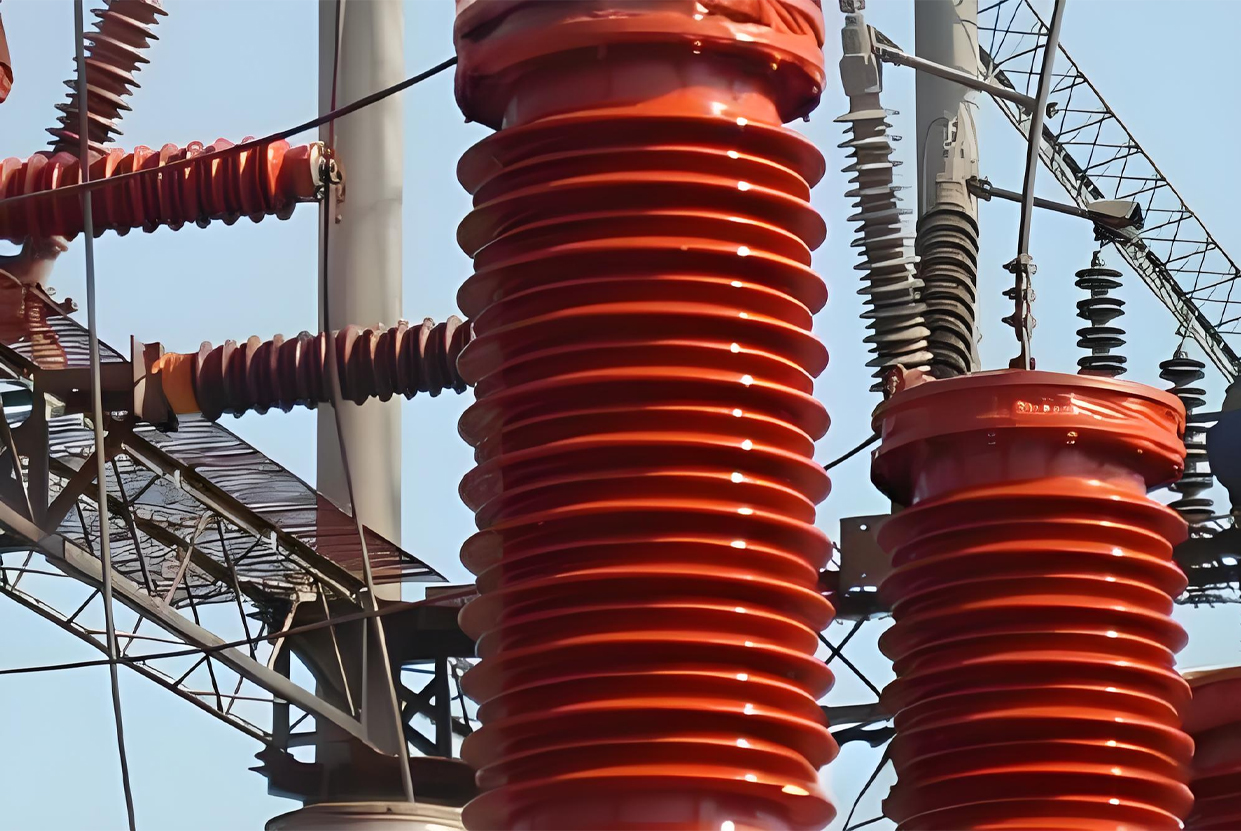
Conclusion
Solid-state silicone injection machines are revolutionizing the way we produce critical components for the power industry. By ensuring the precise manufacturing of high-performance insulators and lightning arresters, these machines help protect our electrical infrastructure from environmental and electrical hazards. As the power industry continues to grow and evolve, these machines will play a crucial role in ensuring that our grids are safe, reliable, and resilient—now and into the future.
If you're in the power industry or involved in manufacturing electrical components, understanding the importance of solid-state silicone injection machines can help you make informed decisions about the technology that drives the products we rely on every day.
Post time: Jan-03-2025