When Tesla’s stock plunged 15% on Tuseday, the headlines focused on Elon Musk and EV demand. But for those of us in manufacturing, the real story lies deeper: **how tech sector volatility is reshaping the rules of supply chain survival** — especially for automotive suppliers like rubber injection molders.
Consider this: Over 60% of a modern EV’s non-metal components rely on precision-molded rubber parts, from battery seals to suspension bushings. When Tesla adjusts production volumes by just 10%, it creates a **$220M ripple effect** across its Tier 2/3 suppliers (McKinsey, 2023).
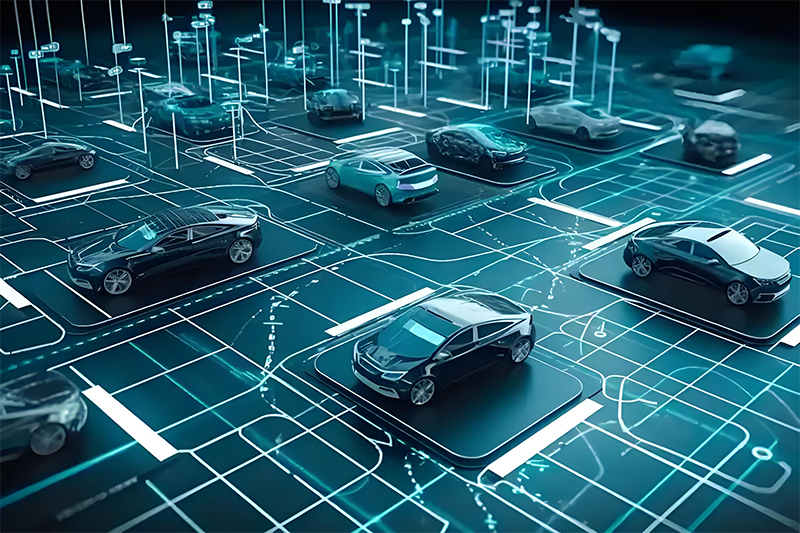
The Squeeze: Where Tech Meets Rubber
The Pivot: 3 Ways Smart Molding Tech Absorbs Shocks
1️⃣ **Demand Whiplash**
OEMs delaying EV projects → 30% shorter lead times demanded from molders
2️⃣ **Cost Crunch**
Raw material volatility + energy hikes → 18% YoY cost pressure
3️⃣ **Inventory Dilemma**
“Just-in-case” vs “just-in-time” – both inflate working capital
**1. AI-Driven Process Optimization**
- Real-time viscosity monitoring cuts scrap rates by 23%
- Self-adjusting clamping force extends mold life 40%
**2. Rapid-Changeover Systems**
- Achieve <15min mold swaps (vs industry avg 90min)
- Case study: Enabling a German molder to serve 3 OEMs on one line
**3. Hybrid Material Compatibility**
- Run recycled rubber compounds at <5% efficiency loss
- Future-proofing for bio-based polymers
Building Chain Immunity: A Supplier’s Playbook
Strategy | ROI Timeline | Risk Mitigated |
Dual-source tooling | 6-8 months | Geopolitical |
Regional micro-hubs | 3-5 months | Logistics |
Digital twin forecasting | Immediate | Demand swings |
The Engineer’s Edge: Where We Co-Innovate
Last month, we partnered with a Tier 1 supplier’s engineering team to:
- Redesign a battery seal module (23% weight reduction)
- Integrate IoT sensors for predictive maintenance
- Cut per-part energy use by 31%
**This isn’t just about machines – it’s about building adaptive systems.**
The next market quake isn’t a question of “if” but “when”. For suppliers ready to leverage:
✅ Modular injection platforms
✅ Open-architecture controls
✅ Data-sharing partnerships
How many production variables does your molding process actively optimize? Let’s discuss in comments.
Post time: Mar-12-2025